Sand-casting bronze-fittings for the Lupine Sabre.
Most of my sword making skills I have taught myself, using experimentation, books and the internet.
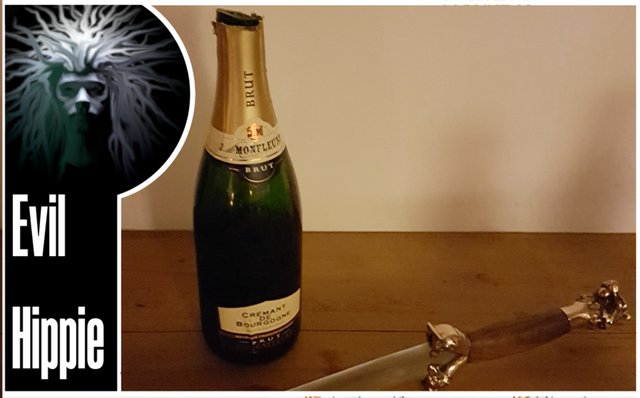
Some of them however I have been taught by others in the course of my education as a goldsmith. One of the skills I learned as an apprentice goldsmith was sandcasting.
It is probably one of the oldest metalworking techniques known to man, and it has not changed significantly in the thousands of years it has existed. The most prominent changes are probably the heat source I use and the way I make my masters(the model used to make the impression in the mold)
My masters for this project are 3d printed and modeled, but they can also sometimes be handmade. I have made a post about sandcasting 3d prints before, but this one will go into more details about the casting process.
I place the model on a flat surface and compact the sand around it, using my hand and a hammer. The sand I use is called delft sand and is a combination of burnt pulverized clay and some king of oil probably kerosene or something similar.
Some people use water moistened sand instead. The upside of water based sand is that it doesn't burst into fire, and it doesn't smoke as much, but it might explode if the sand is too wet, due to the water evaporating explosively. I use the oilbased version because it is what is most readily available in my area.
Apart from the actual hole for the model, I also cut canals for the metal to flow into the mold and for air to flow out.
Since the mold is made of sand I need to be fairly careful when removing the master and putting the two mold-halves together. Small amounts of sand may get brushed of and this can get caught inside the casting - ruining it. Therefore, making the molds are always a slow, slightly nerve wracking, and very concentrated task.
Once the mold is collected it is fairly sturdy. I just need to avoid dropping it, and all should be fine.
Then it is on to heating the bronze. Bronze melts at around 1000 degrees celsius, depending on the alloy, and I need it to get at least 100 degrees warmer than that for it to run smoothly into the mold.
I use a gas-torch for this and to conserve energy, the kiln (which is made of graphite) is put in a small oven made of scamolex plates, fireproof stones and ceramic wool. This picture was taken after the pour so the kiln is already cooled a bit. When I pour, it is a bright yellow, and the metal inside is almost white-hot
As soon as the metal is no longer red-hot I usually remove the upper part of the mold. because the integrity of the sand is compromised by the heat burning the oil, I can usually do this without actually opening the mold.
This gives the bronze time to properly set(if some of it is still molten inside the model) while allowing the heat to dissipate quicker. It also means less of my casting sand gets burned, and since the unburnt sand can be reused this is a good thing.
Then it is the moment of truth. It is always super exciting to break the mold and see if everything has flowed and the casting is complete. As I get more experience the failures are rarer, but only recently I actually forgot to remove the plastic master from inside the mold, which resulted in a destroyed master, a failed casting and a rather obnoxious smelling smoke.
After the casting has been cleaned up and the sprues has been cut of, it is time for polishing and mounting. These fittings were used on my Lupine themed Champagne Sabre and I got to use it shortly after finishing it, since new years eve was coming up.
I can conclude that it works, even when its not a Champagne, but a very nice Cremant de bourgogne instead.
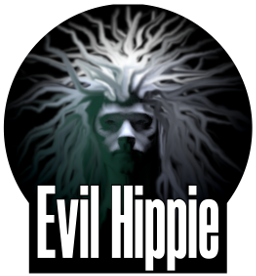
Im EvilHippie, a compulsive creative and jack o' trades. If you want to know more about me, check out my introduction post here
If you like what you see, feel free to upvote, follow and resteem
or you can check out these recent posts
A small handaxe
a nice view revisited
Knives and crypto
Madstedkniv
It came pretty nicely. I hope to see more brass castings. How much shrinkage did you have with respect to the 3d printed model ?
Thanks, sandcastings doesnt shrink noticeably. At least it isnt noticeable for the tolerances I use here. In my experience most of the shrinking in castings happen in the rubber-molds. On the other hand there other issues with precision, such as the sand sliding or crumpling. If you are careful though, you can get a very precise casting
May be a lost PLA with a refractory with plaster can be a good fit for higher precision. It seems to be worth the effort, if the model is not too long to print and you do not mind to destroy it.
lost pla is definitely a possibility but for the fairly simple stuff I do, a multipart mold is fine. I do have the possibility to make investment casting with lost wax etc and also have the possibility to go from print to rubber mold, but then we are back to the problem with shrinking. I do have some castable filament and i also have a resin printer so I can get castable resin, so i am pretty stocked up , as you can see :-)
Congratulations! This post has been upvoted by SteemMakers. We are a community based project that aims to support makers and DIYers on the blockchain in every way possible. Find out more about us on our website: www.steemmakers.com.
If you like our work, please consider upvoting this comment to support the growth of our community. Thank you.
that seems like a nice initiative. I look forward to see how it turns out.
WOW - thats cool - great Workflow ... well done with the casting :-)
resteemed
thanks
Hm, so I like what you're doing, what I don't like is seeing how awesome casting bronze is - I don't need that kind of motivation - I have too much on my plate as it is ;)
Thanks, well if you think thats bad then you should check out this post by olverkieser :-D . But seriously, his stuff is worth a look if you havent discovered him already
Will check him out :)
Art is awesome
Congratulations @evilhippie, this post is the fifth most rewarded post (based on pending payouts) in the last 12 hours written by a User account holder (accounts that hold between 0.1 and 1.0 Mega Vests). The total number of posts by User account holders during this period was 3786 and the total pending payments to posts in this category was $8371.80. To see the full list of highest paid posts across all accounts categories, click here.
If you do not wish to receive these messages in future, please reply stop to this comment.