Exploring Multani Blue Pottery | Kashigari
A Journey Through History and Craftsmanship
The clay used in pot making was historically present in the Indus River and Multan river. Red clay known as terracotta of Multan is very popular. Source
In one of my previous posts, I shared a few glimpses of blue Multani pottery, and at least two of the readers showed interest in it. There is a very rich history in the Indo-Pak subcontinent, and this blue pottery from our city of Sufis, Multan in Pakistan, has its roots tracing back before the partition. While searching and surfing the internet for information on this special craft, I came across some very interesting details. Additionally, I happen to own some pieces of this blue pottery. So here I am, taking you on a virtual tour of this craftsmanship with its very rich history.
Before we begin, let me show you a few pieces that I possess, just to familiarize you with the type of art I'm going to talk about. The name 'blue pottery' comes from the eye-catching cobalt blue dye used to color the pottery. It is also called 'earthen pottery'.
My Collection: The intricate designs on this pottery, known as Kashi or Kashigari, are celebrated for their intriguing patterns, featuring animal motifs, floral patterns, and calligraphy.
HISTORICAL BACKGROUND:
Tomb of Shah Rukn-e-Alam مقبرہ شاہ رکن عالم source
The art of designing pottery, known as Kashigari, has deep roots in southern Punjab, originating from China and spreading through Iran to the Indian subcontinent. Blue pottery, a significant aspect of this tradition, gained prominence with the arrival of experts in Kashigari during the Arab conquest of Multan. The discovery of cobalt oxide revolutionized architecture, particularly Turko-Persian architecture, by providing a vibrant blue pigment. Blue pottery flourished when Shah Abbas of Iran invited artisans from Kashgar (hence the term Kashigari) to refine the craft in Isfahan, eventually spreading to Afghanistan and parts of present-day Pakistan. Multan emerged as a key center for blue pottery, with experts settling in the region and perfecting the art over generations, making blue their preferred color.
The presence of this art in Multan can be traced back to the saints this city is famous for. This is the tomb of Hazrat Shah Rukn e Alam, a shrine that is visited by over 100000 pilgrims every year. Notice the details on the monument, painted in the trademark blue mosaics of Kashigari pottery. No wonder the second most significant cultural export of Multan is blue pottery.
Mausoleum of Tomb Shah Rukn e Alam source
The prevalent blue Kashigari style in historical buildings and shrines overshadows the decorative aspect.
The use of blue color is so evident in the artistry of this Tomb of Shah Gardez, Multan. The ceramic tiles are made from the same principle of Kashigari Source
MAKING OF BLUE POTTERY
This traditional craft involves the use of quartz and fullers earth to create a distinctive type of pottery that is then adorned with intricate blue and white designs.
The skill of creating blue pottery is called Multani Kashi or Multani pottery work which was introduced by the local craftsmen of the Multan region. In 1985, Punjab small industries corporation established an Institute of Blue Pottery Development to save the art from extinction. Blue pottery of Multan is at display in president’s house, prime ministers secretariat, culture missions of Pakistan in different countries and British Museum London.
The modern process of crafting Multani Blue Pottery, from casting to finishing, Kashi to glazing, involves meticulous handcrafting, infusion of vibrant blue tones, and a harmonious blend of tradition with contemporary aesthetics to create each piece.
In this video, the craftsman explains the difference between "kashigari" and "naqashi". The former refers to the making of ceramic "tiles," as I mentioned earlier, while the latter pertains to the decorative process on the inside of buildings. The Kashigari applied to pottery and utensils falls under the former category.
He further explains that this craft was traditionally taught at the age of five. However, the education process faced hindrances. His father took the initiative to compile a written form of this art into a book, enabling younger generations to study and continue this craft. His family has been linked with this craftsmanship for the past 900 years.
This is a tedious process comprising eleven to twelve steps. For convenience, I have categorized them into three steps, based on the families/nature of craftsmen involved in the process.
1. Preparation Stage:
Dough Preparation
Raw materials such as quartz powder, Multani Mitti, waste glass, Katria Gond, and Saaji are used to create a non-sticky dough, which is stored for at least 7-8 hours before use.Mold-Making Process
Artisans create molds out of Plaster of Paris (POP) to cast the blue ceramic objects in the desired shapes and sizes.Products’ Casting
The dough is spread over a base stone and shaped into a spherical chapatti form, then inserted into the molds. Raakh (burnt hardwood dust) is used to fill the mold to achieve precise shapes.Scrubbing
After drying, excess raakh is removed, and the walls of the product are smoothed to ensure uniform thickness.Smoothing
The dried product undergoes a second finishing process to smooth the surface, preparing it for painting.
2. Design and Decoration Stage:
Designing
Designs are hand-painted onto the surface, with artisans creating motifs from their imagination rather than tracing them.Color Mixing
Oxides and Ferro metals are combined with edible gum to create powdered colors for painting.Painting
Designs are filled with oxide colors using fine brushes, with primary colors such as blue, green, yellow, and brown commonly used.Glazing
The object is glazed with a specially prepared solution and exposed to the sun to dry.
3. Finishing and Firing Stage:
Firing
The goods are fired in a closed kiln at temperatures up to 800-850 degrees Fahrenheit for 4-5 hours, then left to cool slowly for 2-3 days.Finishing
The final steps involve removing rough edges, sanding the surface, and inspecting the finished goods before packaging for sale.
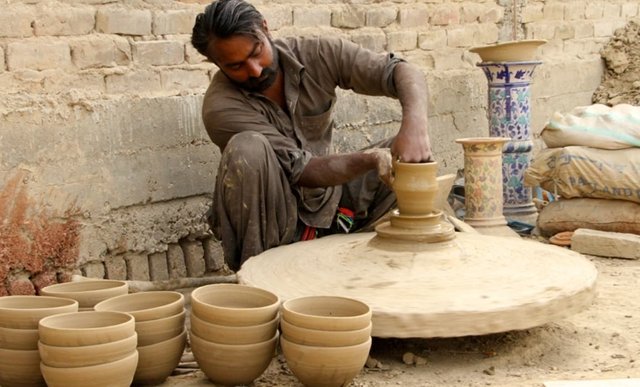
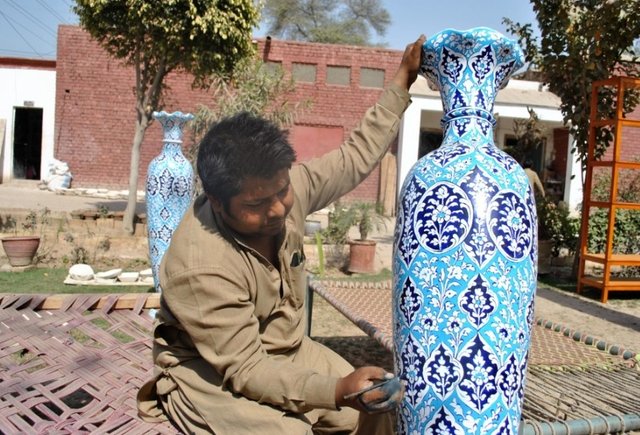
Kumhaar on left & Naqash on right source
The person in the video is explaining another variation, i.e., camel skin lamps that could be made and then painted by "Naqash" (a family he belongs to). These lamps are semi-transparent and they are made in a different way. I would not have understood the process if I hadn't watched this documentary.
The craftsman explains that three families are involved in the whole process.
First, the Naqash draws the pattern of flowers, then the Kumhaar makes the mold according to that drawing. Once the mold dries and the die is removed, casting takes place. After casting, the Dugbour family cleans and creates the masks (made up of camel skin) on the mud mold. After the mask dries in 4-5 days, the inner mold is discarded, giving the craft (e.g., vase) its final shape. It is then painted by the Naqash (referencing the beginning of this paragraph where the role of the Naqash is mentioned).
Source - This handicraft is a merger of two crafts: pottery with skin lamps.
SOME BEAUTIFUL PICKS FOR YOU
Such beautiful vases. One vase depicts Sohni with her matka, a heroine from a tragic folk tale of Punjab. Ironically, she was the daughter of a potter.
These plates are totally to die for
It's fascinating how little this art has diverted from its original style!
Please do share pictures of blue pottery from your origin or from Multan if you have any. I have come across some fascinating facts about different types of blue pottery. I will wait for you in the comments' section. Do come and share about your unique heritage!
Disclaimer:
This article is meticulously researched and heavily sourced to provide accurate information to the best of my abilities. However, despite my efforts, errors or inaccuracies may still occur. I have diligently cited the sources of images and data used in this article, and I have taken measures to ensure that no copyrighted material is included. The majority of images are sourced from advertising sites with proper attribution. The views expressed in this article are solely those of the author and do not necessarily reflect the opinions of any affiliated organizations.
This blue color looks really beautiful. It is not surprising that this traditional art was able to survive for many centuries. However, I thought that blue pottery was now manufactured on an industrial scale with the help of machines. I was wrong, everything is still done by hand, which adds a special value to the products.
This is a really thorough and informative article. I like to learn about the customs of other countries. Thank you. 😀 Your people have something to be proud of.
As far as I know, it is still made by hand.
Thank you for finding it informative. "It was like bottling a river in a tumbler."
I had to omit so much information to keep it readable and maintain concentration spans. Articles like these are the hardest to write. I did another edit an hour before, but I just can't seem to be satisfied... lol
I hope that people find it interesting and relevant. 🤞
You are right. Sometimes I write articles on popular science topics. Preparation of such an article can take two days.
It's worth every minute spent if people find it even a little interesting too. That's my aim whenever I write such things... But then it's all subjective :)
You, on the other hand, have quite a large audience that finds your work interesting.
What a sea of information!
I think I just got a doctorate in blue pottery.
I've been to these mausoleums a couple of times but I could never connect the dots between blue pottery and those tombs. 🫣
Those Camel Skin Lamps....🤩
I love how Steem plays a great role in teaching me new things every day and you sure know how to keep informative articles interesting yet useful all the while.
True, very true. I had a vague idea about the relationship of the blue color used in tiles and their use in shrines and tombs, but honestly, I wasn't well-versed. While exploring and searching, I got to know about so many new things, especially a great deal about history.
And I was totally clueless about the making of these famous camel lamps. A few of my friends have these, and I always wondered how it was possible. I don't see camel skin here.
Thank you millions for stopping by and finding this interesting.
P.S: You forgot to share pictures of your blue pottery. See the last paragraph where I have mentioned:
I know you have a few
TEAM 1
Congratulations! This comment has been upvoted through steemcurator04. We support quality posts , good comments anywhere and any tags.You get ordinary, and then you get extra ordinary.
Well, this post is extra ordinary!
So up my alley!!
Great work!
It's truly rewarding when someone appreciates your hard work.
I spent days collecting the data and then compiling it, including only relevant information. While sourcing my article, I never let go of the personal touch and rewriting 90 percent of the sourced material in my own words. More than writing the post, I spent time editing it. I know too much information can't be bombarded, making it difficult to digest.
Believe me, while the appreciation through upvotes is definitely a perk, I write for comments like yours.
I think most of the information I have shared is available on the internet, but I guess people may find it interesting if compiled in a certain way... Or maybe not. Only the comments can tell!
Thank you millions for visiting this post, despite it being 17 days old.
Well, you did a great job!
I've also said on numerous occasions that the comments are worth far more than the votes when you know that your post was enjoyed, especially after the hard work you've put in.
Like Benjamin Franklin said, "Either write something worth reading or do something worth writing."
a very labour-intensive process. It is good that this tradition and this art have survived to this day.
It is a national treasure and it should be preserved )
Yes, it is. When I researched for my article, I was totally taken aback by the labor and their intensive work. Then, there are different variations of this art.
I have highlighted in my text that there were some steps taken at the government level to sustain this industry.
Thank you so much for stopping by 🥰
I've tried working with clay. You have to do it professionally, otherwise it doesn't work )
Can you show us some of your work?
I'm interested
I didn't actually make anything ))
It didn't even come to firing clay, but I don't have a kiln for firing )).
All that I made with clay is a model of my future sculptures made of wood. A kind of sketch.
But none of that has survived. I still have the clay and I will make something else out of it))))
I see 😊
Your post is manually rewarded by the
World of Xpilar Community Curation Trail
STEEM AUTO OPERATED AND MAINTAINED BY XPILAR TEAM
https://steemit.com/~witnesses vote xpilar.witness
"Become successful with @wox-helpfund!"
If you want to know more click on the link
https://steemit.com/@wox-helpfund ❤️