High Temperature Treatment of Ceramic Wares
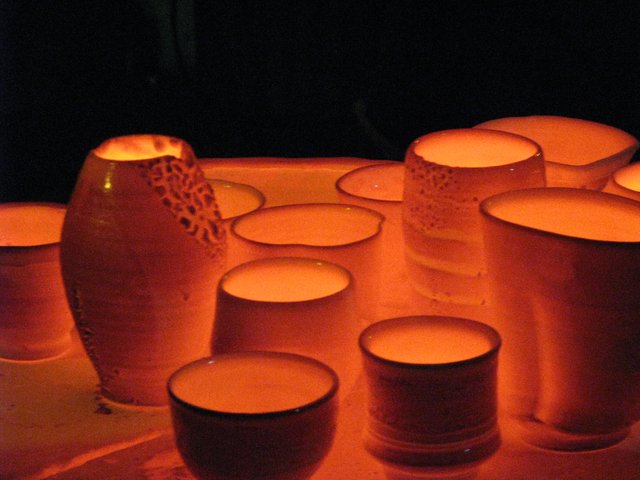
"High Temperature Treatment of Ceramic Wares"
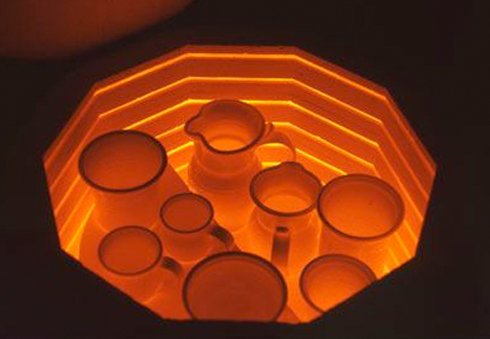
One of the most important stages in manufacturing process of ceramic products is known as the firing or sintering phase which is also known as the high temperature treatment of ceramic wares. It is an important stage in the manufacturing process of ceramic products as the latter developed their final strength during this phase. Partial and complete vitrification may or may not occur during the process depending on the temperature range and the raw material components involved.
Basically during heat treatment procedure the output or the resulting ceramic product obtained its long-term and permanent material properties such as its strength and hardness. The process is usually done in an enclosed chamber but with appropriate exhaust. After the heat treatment stage, firing curve is usually obtained which also shows the temperature of the entire firing process, including soaking and cooling stages.
The firing process includes sintering stage where in the green ware or the initially formed product is heated up to a certain temperature called the firing temperature. The gradual increase of temperature to its limit is also controlled and observed. Other stages in the process include soaking period at certain temperatures and cooling stage after the actual heat treatment process. Firing curve may also be gathered as records as to see hints for improvements of the process.
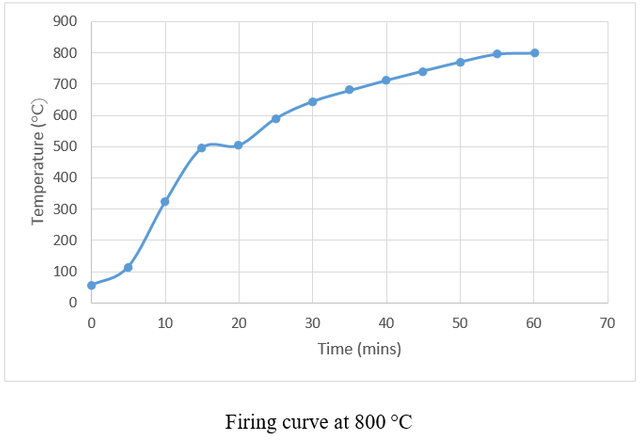
Firing requires experience and it is one of the most difficult stages in the whole ceramic manufacturing process. This the sole reason why plotting of temperature in the form of a firing curve is essential. The temperature inside the kiln is measured using certain types of thermocouple which is then linked to a digital pyrometer. All the inputs such as firing temperature, soaking time at certain temperature etc. are all set in the pyrometer prior to firing.
Generally during the entire process, certain condition especially with regard to the heating rate, firing temperature, soaking period, cooling rate, and also composition of gaseous medium surrounding the product is well documented via the pyrometer except of the composition of present gas. This will help served as the indication and clue when significant discrepancy of output is observed despite uniform batching of raw material components and undeviating initial forming process.
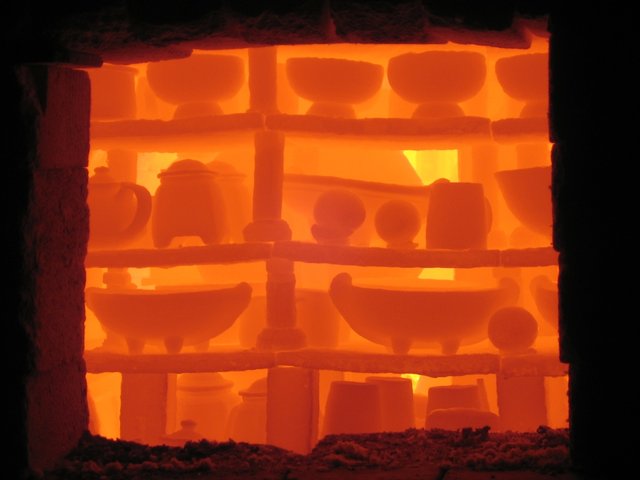
To give an overview, during heating-up period, gradual increase in temperature is necessary to avoid thermal shocking which might result to cracking of products. By controlling the temperature, the stresses that the product experience during thermal expansion and contraction of the product, the changes of state i.e. silica transformation and the combustion of humus or binders do not cause damage to the product.
This is why soaking at certain temperature for a definite period of time is applied. During this stage, the temperature is maintained for some time before gradually increasing it to another temperature which might be slightly above the current temperature. Primarily, the degree of sintering at which the product is subjected depends on the raw material composition, kiln atmosphere and target product output.
During sintering stage or the firing stage, physical deformation under their own weight might occur. This deformation is proportional to the firing temperature and might also become permanent form of the product after the process. Therefore, ideal firing curve is different with respect to the product raw material components and individual composition.
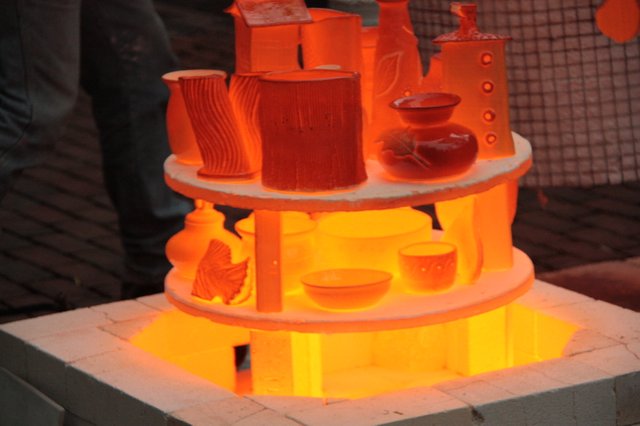
The last stage of the firing process is called the cooling process. Products which successfully endure extreme deformation and stress during the heating stage could still fracture during cooling period. This is where the ceramic products actually obtain their final form and dimension after they set out from warmer state. Excessive cooling could cause breakage and fracture due to undue contraction at certain temperature.
Usually the cooling rates to be applied for safe and rapid cooling depend on the crystallization process of the ceramic product. Temperatures wherein silica transformation occurs are to be observed. Thus the cooling rate might also depend on the crystal conversions in the product and on its thermal contraction.
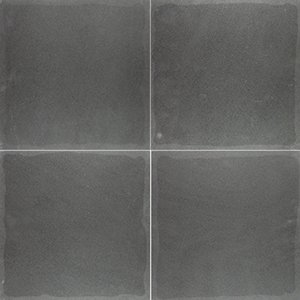
Normally, variation in the heat treatment of ceramic products which are fired simultaneously or successively, whether or not accompanied by fluctuation in the composition of the raw materials may significantly affect the consistency of the quality that the output or fired products have to be sorted or much even be adjusted after firing process and after the outputs are evaluated. Thus synchronized documentation of firing curve and other data is really necessary.
Consequently in the case where these parameters are unmonitored and not well documented, root cause for observable defects are difficult to be traced which will result to irrational or illogical adjustments. It will serve as guide and will also help avoid future interruption due to certain product complications as well as achieve set target and maximize product output.
Although documentations of these certain parameters are not really required, it is still essential when industry needs to be economical and aimed to be profitable. Application of such practice will result to reduce in maintenance cost, downtime during firing process, energy consumption during the entire process as well as maintain product quality.
THANK YOU FOR TAKING THE TIME TO READ MY POST
Importance in Characterization of Raw Material Components and Slurry in Fabrication of Traditional Ceramic Products
Enhancing Low Thermal Insulating Property of Porous Ceramic Raw Materials
Utilization of Local Clay Material in Fabrication of Ceramic Earthenware through Slip Casting Method
Effects of Lightweight Ceramic Materials as Fillers for Paint to Reduce Heat Entry in the Building
High Temperature Superconductive Properties of Ceramic Materials
Advance Ceramic Applications to Automotive Industry
References:
[1]High Temperature Treatment of Wares by Engr. Rechel Jane J. Kikoy, Engr. Christian Volter G. Ranada, March 2014
[2]Susan Peterson, Jan Peterson, The Craft and Art of Clay: A Complete Potter's Handbook, retrieved March 2014

Nice detailed article on the baking process of Ceramic articles. Also read your previous articles on the topic. Really informative and learnt a lot about the process.
Keep it up bro. :)
Thank you so much for you kind words. I am glad you have learned from it.
Very accurate and stated as only a ceramic engineer can! As a ceramic artist all of this is familiar and interesting to read a description from a different part of the industry.
Thank you for your kind words.
I find this very interesting @asbonclz. My dad used to work in a refractories plant. :)
Ceramic wares have a rich history of craftsmanship and artistry, offering a myriad of practical and decorative possibilities. From exquisite hand-painted pottery to delicate porcelain creations, ceramic wares have long held a special place in our homes and hearts. They bring beauty and functionality together in the most elegant way, with each piece telling a unique story through its design and craftsmanship. For those seeking to explore the world of ceramic wares and acquire these timeless treasures, a visit to https://cosmosartceramics.com/ unveils a world of stunning options and opportunities. Here, you can discover an array of beautifully crafted ceramic wares that add a touch of sophistication and artistry to your living spaces, making them as functional as they are aesthetically pleasing. Whether you're an enthusiast, a collector, or simply someone looking to elevate your home decor, ceramic wares offer an enduring allure that transcends time and trends, and Cosmos Art Ceramics is your gateway to this timeless world of craftsmanship.