Utilization of Local Clay Material in Fabrication of Ceramic Earthenware through Slip Casting Method
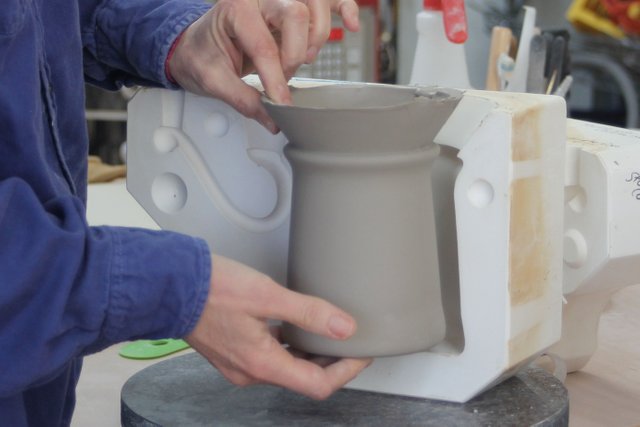
"Utilization of Local Clay Material in Fabrication of Ceramic Earthenware through Slip Casting Method"
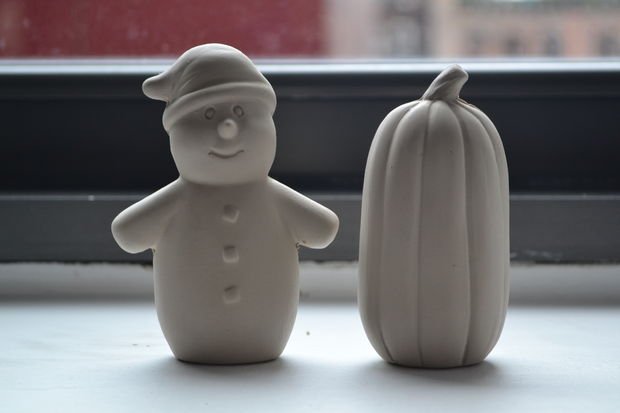
The production of ceramic earthenware in the Philippines is the most common small-scale industrial business in ceramic industry. Earthenware non-vitreous porous ceramic products which are usually fired at lower temperature than the usual firing at around 800 to 1000 degrees Celsius. Earthenware ceramic products have good thermal insulating properties, are brittle and softer than most ceramic products due to their porous structure
Earthenware has high water absorption at around 5% to 8%. They are generally glazed to cover their porosity when used as kitchen wares. Technically, earthenware products are terracotta in color due to the high amount of iron oxide impurities. Ordinary earthenware products such as bricks, jar and pot are usually produced with mere local clayey raw materials and silica. They can be easily formed too and due to their cheap body formulations, small-scale businessmen find it as ideal industry.
Clayey raw materials are naturally abundant in earth’s surface. Hence during my academic years, we (together with my colleagues) are tasked to utilize local raw materials to produce decorative ceramic earthenware. Our objective was to put economic value on local raw materials as well as to provide formulation for local residents for them to be able to utilize their own minerals for industrial business.
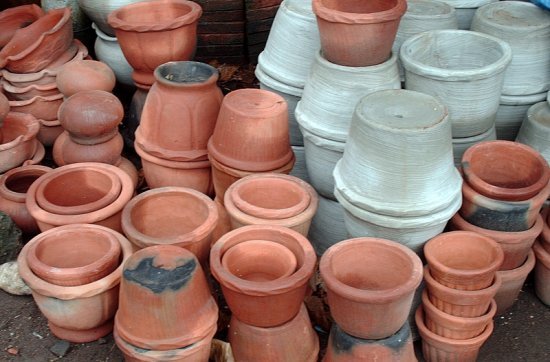
Most earthenware products are formed using usual forming methods such as molding, coiling and throwing. You can read my article regarding the various forming methods of ceramic products here. However, due to the complexity of the design that we desired to produce, we instead fabricated our decorative earthenware product by means of slip casting method which is a more convenient method of producing products with complex design.
Slip casting method is a forming technique which uses gypsum mold which is made out of plaster of Paris and water. It also utilizes slurry or slip which is a type of ceramic body formulation with high amount of water and low but controlled viscosity or in other words, a suspension of clay particles in water. With this method, the slurry is poured unto the gypsum hold to form your desired product design. The thickness of your product depends upon your experimented settling time based on your preference.
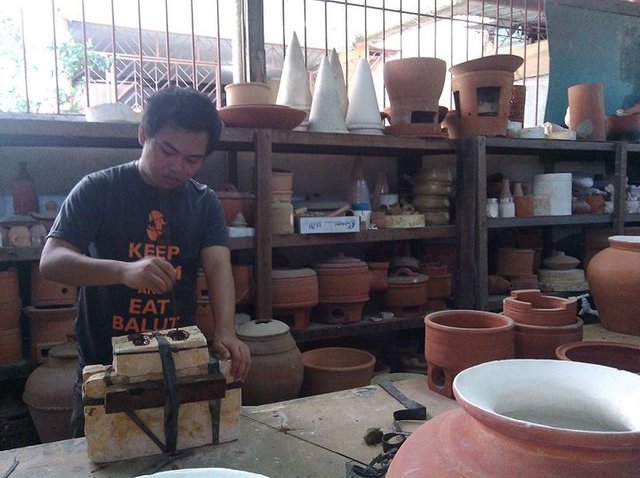
We first visited the area and quarried sufficient amount local clay raw materials for the experiment. The excavated raw material (clay) underwent characterization and beneficiation process. By this, it means that the physical properties such as the density, particle size distribution, drying and firing shrinkage, loss on ignition (LOI) etc. were determined and obtained. Various formulation of body components were then made based on the obtained physical properties of the local raw material.
After thorough experimentation, an ideal and economical body formulation was finalized. Our slurry or slip formulation is comprised respectively of 40 wt% and 60 wt% of locally acquired red clay and silica. The amount of water and deflocculant (or the dispersing agent) added were based on the desired rheological properties that we determined earlier. These rheological properties such as the viscosity and thixotropy were determined and controlled as they influenced the greenware formation during casting.
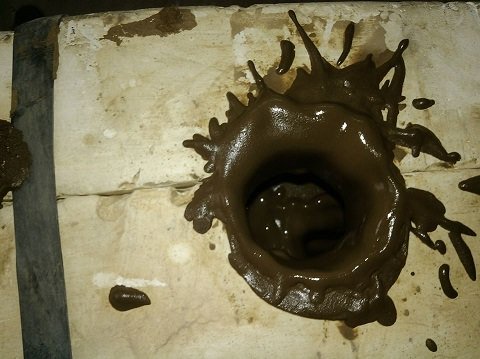
The specific gravity of the slurry was also controlled between 1.70 to 1.80 grams per cubic centimeter. During casting (or pouring of slurry to gypsum mold), the slip is gradually poured unto the cavity of the mold and is then permitted to settle for minutes depending on the target thickness of the desired product. We set our casting time at 30 minutes its corresponding thickness is 5.20 mm. Therefore, after 30 minutes, the excess slurry was poured out of the gypsum mold and the initially form product is removed afterwards.
The resulting greenwares are airdried for 24 hours and was oven dried at 100 degrees Celsius until constant weight was attained. The average drying shrinkage was obtained to be 5.07%. Subsequently, the dried greenwares were fired at 800 degrees Celsius. The average firing shrinkage and the average loss on ignition of the final product were 0.77% and 9.8% respectively. We successfully produced decorative ceramic earthenware out of local red clay raw materials and sand as the primary source of silica.
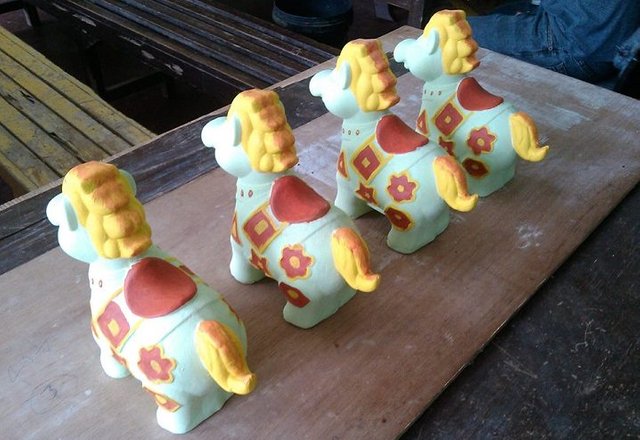
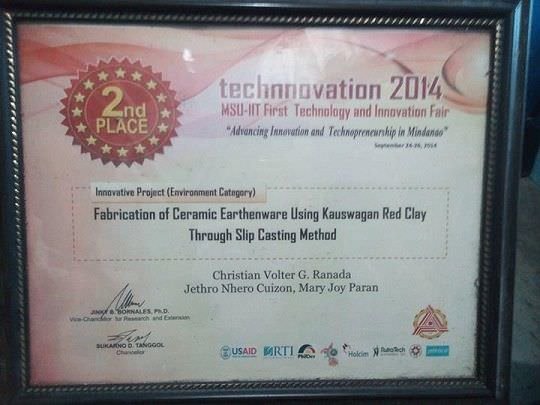
Our research project has also won 2nd place as best Innovative Project in Environment Category during the First Technology and Innovation Fair last September 26, 2014 at Mindanao State University – Iligan Institute of Technology in Iligan City. We received as small amount as prize for our works. And as we Filipinos are fond of eating, we spent our incentives eating the most satisfying food to reward ourselves for a job well done.
THANK YOU FOR TAKING THE TIME TO READ MY POST
Effects of Lightweight Ceramic Materials as Fillers for Paint to Reduce Heat Entry in the Building
High Temperature Superconductive Properties of Ceramic Materials
Advance Ceramic Applications to Automotive Industry
Advance Ceramics Application to Electronics Industry
An Overview to the Manufacturing Process of Flat Glasses
Reference:
Fabrication of Ceramic Earthenware Using Kauswagan Red Clay Through Slip Casting Method by Researchers Christian Volter Ranada, Jethro Nhero Cuizon and Mary Joy Paran

wonderful post.. thank you for shahring
Wow, you read too fast, I just posted it.
thanks
a very beautiful job my opinion.
This is creative, amazing, i would give it a try!!
Awesome post. You really did a great job with ceramic.
Really very much informative post suggesting a nice method for the fabrication of ceramic products.
Keep it up. And thanks for sharing. :)
Congratulations @asbonclz! You have completed some achievement on Steemit and have been rewarded with new badge(s) :
Click on any badge to view your own Board of Honor on SteemitBoard.
For more information about SteemitBoard, click here
If you no longer want to receive notifications, reply to this comment with the word
STOP
Your research gave out a splendid article. As always. great job!
Your post has been upvoted and resteemed by the @bayanihan curation team.