Classification of Refractories According to Physical Form, Method of Manufacture and Chemical Nature

"Classification of Refractories According to Physical Form, Method of Manufacture and Chemical Nature"
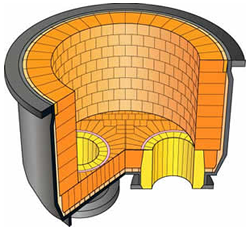
From my previous article yesterday, we’ve learned that refractories are materials used to isolate the high temperature inside heating chamber which also helped minimize heat loss. Refractory materials have a very high melting point which means that it can withstand very high temperature. Due to this fact, refractories are commonly used by steel and ceramic industries to act as heat barriers between high and low temperature zones. Refractories are also classified accordingly based on numerous factors. However, refractories are used more than just heat barriers.
Refractories are installed in high temperature furnaces to protect walls of heating chambers and prevent weakening and damage during heating process. Furthermore, refractories are also set up to act as chemical protective barriers against corrosion and any chemical attack during the same process. With respect to the operating environment, refractories should be efficient to resist any possible and specific heating behavioral conditions.
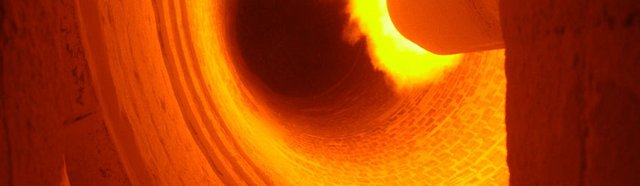
Different industries with different products have different requirements and standard for the use of refractories. Therefore it is necessary for refractory manufacturers to produce refractories with various properties to meet range of processing conditions. Refractory materials are not just adjudicated by mere melting temperature and manufacturing costs but by its performance under specific condition. Also, the qualities of refractories are dependent to its physical and chemical properties.
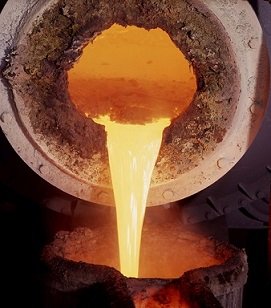
Therefore, refractory use is dependent on the nature and condition of the operating environment they’re applied. Hence refractories should be selected depending on the operating environment they’ll be used. Engineers continually developed refractory materials which are suitable and compatible for various and/or specific application and industry. Refractories are then classified accordingly based on the chemical properties of their constituents or components, refractoriness and strength, physical form and method of manufacture.
Refractories are basically classified based on the manufacturing method it undergoes prior to utilization in various industries. In general, refractories can be manufactured through Dry Pressing Process, Fused Casting Method, and Hand Molding. Refractories are also manufactured either as Formed or Unformed materials. Formed refractories are refractories with definite shape upon manufacture while unformed refractories do not have definite shapes. Refractories are also classified based on the physical form after manufacturing process.
Refractories are generally classified based on their physical form namely shaped refractories and unshaped refractories. Shaped refractories are most commonly known as refractory bricks with standard dimensions while unshaped bricks are known as monolithic refractories. These individual refractories are specifically used for particular kilns and furnaces and according to distinct purposes.
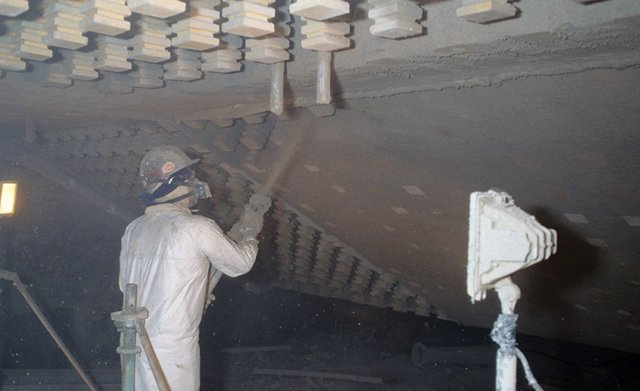
Shaped Refractories are those with actual and fixed shape after production and are commonly rectangular in shapes and figures. Unshaped Refractories alternatively are those refractories without definite shape or form after production and are commonly applied and installed to kilns and furnaces through casting, spraying etc. Both refractories have also distinction according to the type of furnace they are installed unto. Both have also specific advantages and disadvantages.
Technically, refractories are classified based on their chemical reaction and behavior during heating process inside heating chamber. And according to source, refractories are mainly made out of single or multi-components of inorganic compounds with non-metallic elements. According to chemical composition and nature, refractories are classified as acid, basic or neutral refractories.
Acid Refractories are refractories which are not affected by acidic materials and are primarily used to counter chemical reaction and chemical attacks by alkali compounds and elements or by the basic slags. These refractories are used in chamber or zones where the atmospheres and slag reactions are acidic. Most common acidic refractories are silica, zirconia and aluminosilicate.
Basic Refractories on the other hand are refractories which are stable to alkaline slags and therefore are not affected by basic slags, dusts and fumes at high temperatures. Opposite to acidic refractory, these types of refractories are technically used in furnaces where the operating environment is alkaline. Most common raw materials for basic refractories are magnesia, dolomite and chromite.
Neutral Refractories are refractories which are chemically stable to both acidic and basic atmospheres. Hence, these types of refractories are used to areas where the slag and atmosphere are either basic or acidic. The most common raw materials for neutral refractories are carbon graphite, chromia and alumina.
THANK YOU FOR TAKING THE TIME TO READ MY POST
Ceramic Application to High Temperature Furnaces as Refractory Materials
A Quick Overview of Ceramic Glaze to Ceramic Products
Electric Mosquito Net with Silica Fabric (Ceramic) Insulator
Don't Miss This Year's Orionid Meteor Shower!
References:
Introduction to Refractories Chapter 12 pdf
Refractories: Introduction to Refractories by Dr. Hussein Alaa
LECTURE 9 Refractory Materials pdf
Refractory Manufacturing pdf
Introduction to Ceramics, Glass and Refractories by Dr. Kassim Al-Joubory

So informative Up. :)
Salamat up! :)
great post @asbonclz. upvote this comment to grow me up.
My steemph support!