Stages of construction work
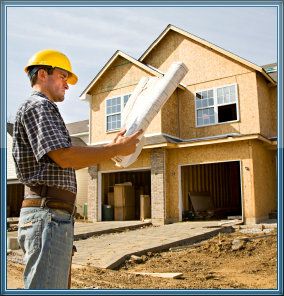
The foundation Stone Mountain
excavation of stone foundation times
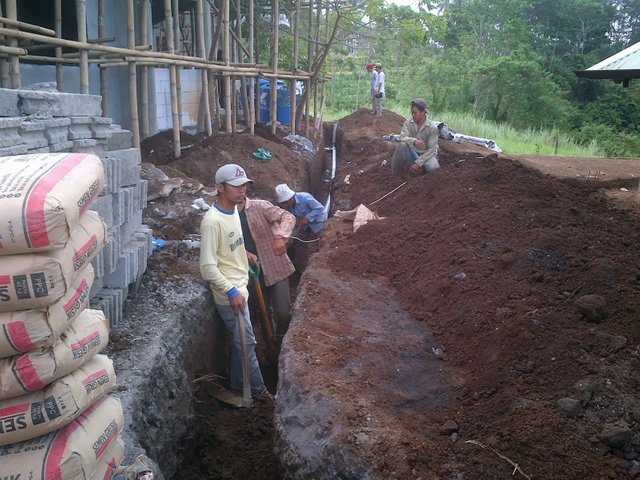
Pedestal Sand Backfill
Empty Stone Pairs
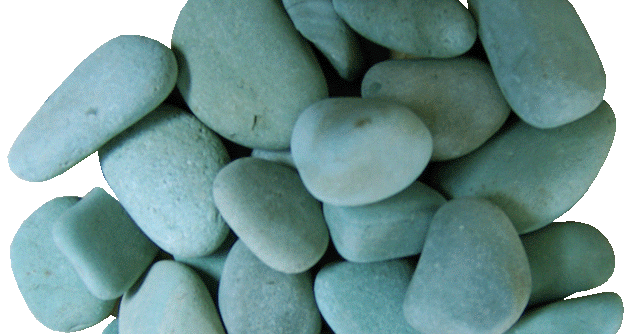
The foundation pairs (Stone Mountain)
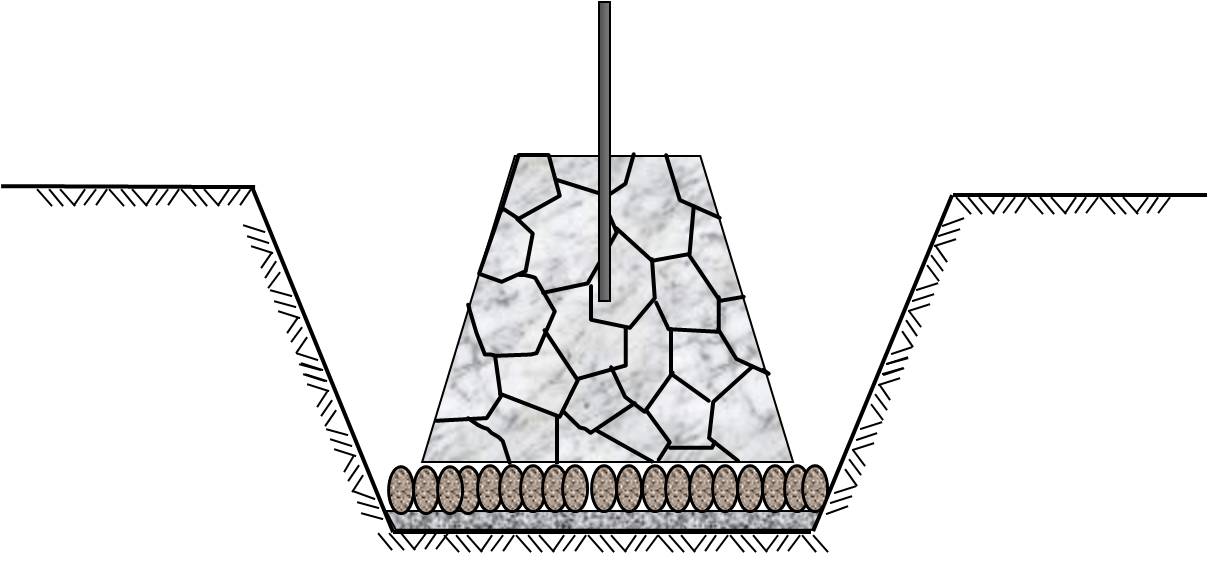
Anchor Diameter 8 - 100 cm
Anchor iron mounted field must be in accordance with the needs of the job, Installation of Anchor Stick diameter of 8 mm in accordance with the drawing plan. The production of the main reinforcement and bearing reinforcement for each work item is adjusted to the diameter, number and distance of the reinforcement based on the plan drawing, the equipment used for this work includes iron scissors, pliers, iron bolts, gauges and others.
If the reinforcement with a predetermined size does not exist / it is difficult to obtain then we will submit a written permit request which is attached with the plan of change along with the technical calculation and the implementation period, The implementation of the reinforcement (bending connections, cross-reinforcement installations, etc.) must comply with PBI 1971, before casting the reinforcement circuit shall be equipped with concrete decking (concrete tofu) with a minimum thickness of 3 cm, placement and quality must be approved by the supervisory consultant and the Board of Directors. The reinforcing steel to be used up to the time of casting must be free of dirt, grease and rust and other impurities that can reduce the adhesiveness between the concrete and the reinforcement mixtures.
Pouring back the former excavation
Excavated pouring work is done with the material of excavated soil, and the soil is first cleaned of dirt and wood former formwork, The casting is done several layers, then each layer is obtained by means of compactor and others.
Landfill
Heap material, we will bring to the location of work that has met the technical specifications and the approval of the directors, which we then transport by using the Dump Truck and then spread at the landfill or work location, the compaction of landfill by way of flattened using the tool, ground leveling work is the result Land heap imported.
Materials needed include:
Formwork
- Cement portland type I according to SNI-8 in 1972 and meet the s-400 according to Cement poladia standard outlined by the Indonesian cement association (SNI-8 in 1972), cement storage will be stored in such a way so as not to harden, cement storage we will raise 30cm And the stack is 2 cm tall.
- Natural sand with a mud content of less than 5%, sand quality will meet the requirements of SNI 03-246-1991 or P.B.I 1971, the sand consists of clean, sharp grains and free of organic materials, soil, mud and so on.
- Pebbles with a maximum diameter of 25 mm, fine grain content of less than 1 percent.
- Rock mountains (for mountain rocks used in concrete pairs of foundations of mountain rock 1: 3: 5)
- Water for stirring concrete does not contain oil, acid and alkali and gram so it can damage the quality of concrete.
- Iron concrete in accordance with the bestek image, the steel quality used is U-24 for diameter <13 (minimum karateristic neck stress 2400 kg / cm2), iron concrete stored not touching the ground and should not be stored for long periods of time, cut or bent reinforcement shall be subject to the approval of the technical director.
- Wood and board suitable for formwork requirements.
- Production formwork adapted to the type of work that is foundation, column, sloof, beam floor and beam ring.
- Formwork is manufactured from 9 mm multiplek material and 5/7 wood according to the shape and size with production amount of each work approximately 40% of the formwork requirement (foundation, sloof and column) whereas for formwork floor beams and plates are produced 100% for speed up the execution time and specifically for floor plates used multiplek 12 mm so that the floor plate is not curved.
- Installation of formwork done before or after iron installation, this is done in accordance with the needs of each job.
- Setting the formwork done after formwork attached reinforced with 5/7 wood support so that the formwork strong, neat upright and in line.
- Equipment used for this work include saws, drills, hammers, crowbars, untings, crabs, hoses, threads, waterpass, gauges and others.
- The quality of concrete used is Concrete K-225 comparison 1 cement: 2 sand: 3 pebbles.
- Preparation of Prints and References comply with the provisions of 5.1 of SK. SNI T-15.1991.03.
Iron assembly
- Production of iron to be installed in the field tailored to the needs of work such as foundation, column, sloof, ladder, beam, ring balk and floor plate in accordance with bestek drawings.
- Production is conducted in work barracks supervised by contractor inspectors and approved by supervisory consultants and directors.
- Production of base and begel reinforcement for each work item is adjusted to the diameter, number and distance of reinforcement based on the bestek image.
- Equipment used for this work include iron scissors, pliers, steel bends, gauges and others
Casting
- The foundry is done after the formwork and iron has been installed, and before casting it is necessary to check again the formwork and iron to avoid any errors in the implementation. Prior to the foundry should be reported to the supervisory consultant for foundry approval.
- Prepare tools and materials ie concrete mixer, cement type I, natural sand and gravel and water in accordance with the needs of casting volume.
- Especially for plate floor and beams are planned casting using preparing tools and materials that is concrete mixer, type I cement, natural sand and gravel and water in accordance with the needs of casting volume.
- Prepare a mixed proportion based on the results of the laboratory mix design for the specified quality of the concrete.
- Stirring is done with conrete mixer until the mixture is completely flat, homogeneous and thickness of slurry in accordance with mix design, this work will be supervised by quality control personnel.
- Sampling / cubes 15 x 15 x 15 cm to determine the quality control of concrete in accordance with SNI 91. Sample is taken for each reinforced concrete item and tested the compressive strength of the laboratory when the concrete reaches 7 and 28 days.
- Pour the concrete into the mold and when the concrete mixture is poured concrete compacting with a concrete vibrator tool, in order to obtain a solid concrete that is not porous.
- If there is an old concrete connection and the new concrete then on the old concrete surface is marketed when the concrete is continued then the connection is given a cement paste with fas 0,3 so that the old concrete with new concrete binding well.
- All stages of the work are supervised by the executing supervisor and approved by the supervisory consultant and the board of directors.
Equipment used for this work include concrete mixer, concrete vibrator, barrel size, stroller, shovel, hoe, bucket, concrete lift (specially for casting upstairs), slump test, cube mold, meter and others.
Creating Concrete Sloof
The reinforcing pairs that have been produced in the work barracks (the number of reinforcing bars, and the bearing distance) shall be in accordance with the drawing of the plan.
Installation of previously manufactured formwork, in accordance with the size of the sloof and side-supported pairs as binder. Installation should be straight and strong so it does not expand at the time of casting. The casting corresponds to the proportion of the mixture.
Creating Concrete Columns
Marking and shoe columns to fit on the specified axes in accordance with the plan drawing. Installation of the column as well as equipped with begel in accordance with the picture. Attach the column formwork to the four sides (formerly formwork smeared oil) and reinforced with 5/7 reinforcing wood on all sides of the column, as well as side support on the four sides of the column. setting the columns in a way in the top-down lot to get the column stiffen and when the support is immediately locked. Installation of spacer concrete on the top so that the concrete blanket in accordance with the drawing plan. Determine the foundry limit is by installing a nail on the wall formwork, so that at the time of casting the column height is not excess or less than the size of the drawing plan.
Creating Concrete Beam
The beam serves to keep the vertical load at the top, if there is a hole in the wall work. Beams consist of several sizes. Top of Bearn, or the top side of the beam follows the height of the roof plate. In the implementation, an implementer must be proficient and understand the technique of repetition, because it has reinforcement and reinforcement field.
Reinforcement has the following characteristics:
- Located in the ¼ of the base span
- The upper reinforcement is usually more.
- Begel / iron stirrings getting tight
The field reinforcement has the following characteristics: - Located in the middle half of the span.
- Bottom reinforcement is usually more.
- Begel / iron stirrups wider than the pedestal.
Scaffolding
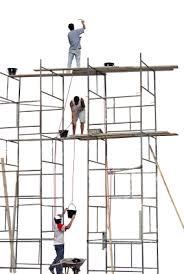
Formwork.
Beskisting plate and cultivated beam made of plywood 9 mm and in its activities can be used in subsequent work. Maximum usage is 2 times usage, so if it has exceeded 2 times need to get approval from the board of directors.
When making formwork plates to note is the elevation of the bottom of the beam and plate, otherwise it should be considered and discussed with field directors where the points will be installed conduit / sparing both electro and plumbing. So it does not happen again after discharging because it will disrupt the stability of the bearing capacity of the concrete.
Spawning
In the implementation of the enlargement of special attention, because of the size and type of iron, the distances become the reference point. The lower beam enlargement should not touch the formwork where the concrete blanket is at least 5 cm in need of concrete decking. The iron used in accordance with the drawings of the plan. Each shipment needs to be attached a certificate as the first control that the material is submitted in accordance with the plan drawing.
If doubtful of the certificate can be proven by iron tests in the laboratory in accordance with the applicable technical regulations where every 10,000 kg is made 1 slimping test.
Casting
Foundry using concrete Mixer K-225 and K-175 and assisted with aids to reach remote areas such as stroller.
Controls:
Concrete curring or concrete watering needs to be done for 7 consecutive days in the morning and afternoon to keep the concrete moisture so as not to extreme in shrinkage that cause cracking of hair or other leaks specially for plate no damping needs to be done to anticipate concrete leak, Unwanted things will be consulted with the directors of the field to obtain effective and efficient direction.
Demolition of the formwork is done 2 days, the vertical formwork can be removed, after 7 days some of the scaffolding can be opened except the scaffold that hold the load directly / above the beam, after 14 days where the concrete strength has reached 75% the scaffolding can be opened except the area under the main beam / Shoulder the main load. On the 21st day new whole formwork can be opened.
Thank you for visiting my blog,I will continue our discussion on another occasion, forgive me all my imperfect writing, also thanks to all the #aceh steemit community who always support me.
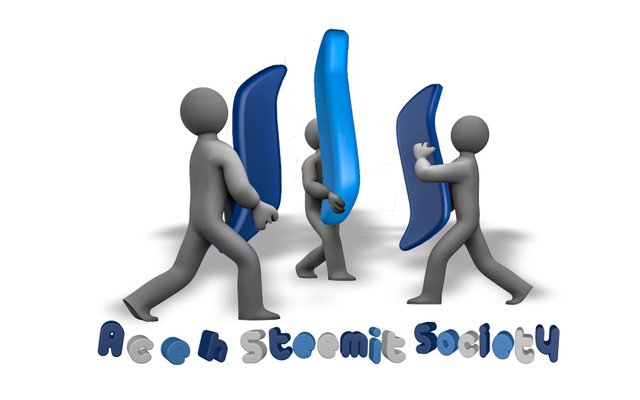
source:
secsiandymanpower.blogspot.co.id
Regulation of reinforced concrete Indonesia
I also invite friends to visit my other blog:
Regards @kharrazi
Meep