The Demigods of Manufacturing (Cutting Tools)
In my previous post on machining, I talked about cutting tools and how they are positioned in the tool post machine or reshape materials into machine parts. Cutting tools are like the basic ingredient used in machining and without them, machine parts cannot be formed. The cutting tool has some great properties embedded in them which were explained in my previous post they are hot hardness, wear resistance, corrosion resistance, and toughness.
These properties are what makes them different from the material the machinist has placed in the spindle, they allow the machinist to enjoy what they do with their materials. You can read all about them here
I stopped there by mentioning some materials used in making cutting tools, but I didn’t discuss what they are made of or why they are like that, so I would start by discussing them one after the other
The plain steel carbon
The plain steel carbon is the earliest form of tool used in machining operation about a hundred years ago in the early days of machining. These tools are made of a high percentage of carbon content which gives the tool its hardness thereby giving the tool a resistance to abrasive wear when machining. But the problem with this tool is that it lacks the property of hot hardness i.e. it gets really hot at even low temperatures therefore they are no longer in use for hot heat applications but rather low heat applications.
They are now found in your files and chisels we take about, of course, those tools are not used at high temperatures.
High-speed tool steel
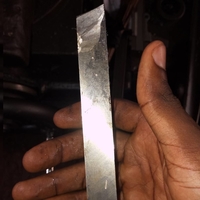
HSS cutting tool : image taken by me @adetola
Where the plain steel carbon had failed (i.e. hot hardness) there was a need to improve on the weaknesses of the plain steel carbon so an upgrade was made which brought about the high-speed steel carbon. These tools were known to withstand heat and high temperatures at high cutting speeds. What if I told you that additives are the only difference between the plain steel carbon and the high-speed tool carbon?
The two main additives to the plain steel carbon gave room for two types of high-speed tool carbon and they were popularly called the M and T series. The M stands for molybdenum and the T stands for tungsten. Other elements added as additives to the high-speed tool carbon include vanadium, chromium, niobium, and cobalt. These additives helped improve the hardening ability, resistance, and strength of the tool.
Cemented tungsten carbide
These materials were founded way back by a man called Henri Moissan in the late 18th century (1893). While he was making a research on creating artificial diamonds. The man recorded that the material, (tungsten carbide) was very hard, it was near that of diamond and surpassed that of sapphire but was very heavy (about 16 times heavier than water). It was later proved that they were brittle hence it limited their industrial usage.
There are several coating materials or elements that can be used for different applications of the tungsten carbide some are:
- Titanium carbide
- Titanium nitride
- Ceramic coating
- Diamond coating
- Titanium carbo-nitride
The ceramic and cement tools
The common tool called ceramic aluminum oxide which is a type of ceramic cutting tool was developed in Germany in the year 1940 (it might not be exact though). The word cement was coined from two materials which are ceramic and ceramic and metal, and the metal is mostly titanium carbide. Although ceramic may be brittle (i.e. break easily) but they have high resistance to hot temperature (hot hardness) this makes them improved upon in making cutting tool and also makes them. The ceramic tools have their importance and application in some parts such as application in light cuts for some very hard materials, they have high resistance to abrasive wear making them important, their extremely high hot hardness is also an advantage to them.
Diamond, CBN, and whisker-reinforced tools
Imagine using diamond as a cutting tool or we in our workshop using diamond as a cutting tool. We wouldn’t even spend up to 10 minutes on any work before the tool goes missing. Well, not that diamond isn’t hard or strong enough to do the job it is great as it is made up of pure carbon. But the ones used in machining are of industrial grade and diamond tools are used for light finishing.
Cubic boron nitride or CBN as you prefer to call them are similar to diamond by their structure (polycrystalline). They are mostly used where the machine tools are very hard (i.e. on difficult to machine materials). Another use of the CBN is that they can be used as a finishing tool.
The whisker-reinforced materials are just materials used to improve the performance and embedded properties of cutting tools. Some of these materials are silicon nitride and aluminum nitride.
Selection of tools
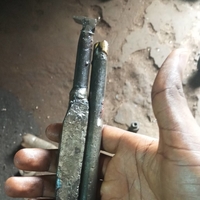
selection of tools: image taken by me @adetola
Right now, I can bet you are asking yourself or about to ask me which one of the tools is the best tool?
But I don’t have an answer for you the best tool should be selected according to the type of material you are about to machine. For instance, the most common tool we use around us is the High-speed steel tool (H.S.S) this is because most of the materials we use are handled well by this cutting tool. This is why we have them around us, but I want you to keep this in mind that the best tool is not always the most expensive tool or hardest tool, but rather the most suitable tool.
You can’t just pick up a diamond tool to machine a plastic, first, it would be foolish getting such an expensive tool just to machine a cheap material like plastic in an unsecured environment. But plain carbon steel is enough for plastic as they are much cheaper and readily available to machine plastic.
The parts of a cutting tool
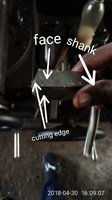
cutting tool parts: image taken by me @adetola
There are different parts of a single point cutting tool which are labeled in the picture below and these parts are the shank, cutting edge, and the face. I have decided to stop there for those who are enjoying this but do not understand our mechanical terms.
The shank is the part buried in the tool post while the cutting edge is an important part of the tool as it does the cutting of the material. The face of the tool is where the chips sit on first before they fall off, they are also used for cutting.
Reduction of friction on the tool
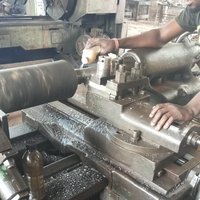
cutting fluid applied to tool surface: image taken by me @adetola
If you read my previous post where I talked about the hot hardness I mentioned that a tool could get as hot as 300 degrees, now that is really bad for the skin if the chip touches your eyes or your body. To prevent this hazard from happening a fluid is added to the surface of a tool during its operation and this fluid is called a coolant.
Well, I am not talking about the one in your car or engine although their jobs are similar, the coolants are different. It is a kind of oil-water emulsion used to lubricate the surface of tools and reduce the temperature of the cutting tool. There are several types of coolants from the pastes to the plant oils and animal fat, but the coolant used in our workshop is an oil-water emulsion coolant which requires you adding water before application. It is whitish, and we apply it manually and directly to the surface of the cutting tool. The coolant could also be referred to as the cutting fluid.
Shaping of tools
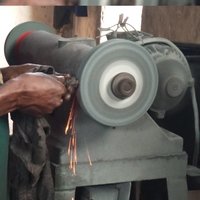
shaping of cutting tool: image taken by me @adetola
The first time I saw a cutting tool the first question I asked is are these bars going to be the one going to make this bend or these small cuts?
The experience machinist laughed at me as he took the tool down to a place and came back with a shaped tool I asked how?
Machine tools are like the metal bars it is just a long rectangular cube when they are first brought in and they need to be reshaped to carry out their jobs properly. This is where certain operations come in. for a strong tool to be reshaped, it may look hard to get them into the required shape you need but it is very easy to do so with some machines in the workshop.
The grinding machine with a cutting disk can be used to cut the new cutting tool into shape by repeated action and holding the cutting tool with a vice to prevent injuries. This could take a lot of time, but it will eventually get them into shape. The use of both the hand grinders and table grinding machine are allowed.
watch this video to see how tools are shaped
Conclusion
The cutting tools are essential in machining as they are required in shaping and reproduction of machine parts depending on the properties of the parts one is about to machine; the cutting tool is selected appropriately to save money for the machinist.
The different parts of the cutting tool have different functions which they are used for which has been discussed also the cutting tool picks up so much heat when doing their jobs that they are cooled using the coolants. Cutting tools are shaped themselves with the use of grinders.
The point is without these little things called the cutting tools, the lathe machine would be useless and just be a toy for rotating parts, therefore as a machinist more focus should be on these little giants that shape other strong machine parts.
Thanks for reading!
References
Here are the books used to gain knowledge about the machine tools and the links.
- Cutting tool applications by George Schneider, Jr. Cmfge
- Geometry of single-point turning tools and drills, Fundamentals and practical applications by Astakhov, V.P
- machine tools
- Manufacturing Process II
- wiki steel
- material removal methods
- wiki - cermented carbide
- the cutting tool, a proof iron sharpens iron
all images and videos in this post were taken and created by my infinix zero five.
If you write STEM (Science, Technology, Engineering, and Mathematics) related posts, consider joining #steemSTEM on steemit chat or discord here. If you are from Nigeria, you may want to include the #stemng tag in your post. You can visit this blog by @stemng for more details.
What properties must a cutting fluid have?
Overall, have done an excellent job on this article.
The cutting fluid have to have High thermal conductivity for cooling, Good lubricating qualities, a high flash point, and should not entail a fire hazard, also they must not produce a gummy or solid precipitate at ordinary working temperatures.
These are just a few. Thanks for the comments.
Thanks for the quick response.
I suppose we should now begin to call you "steemit machinist". You have done more than enough in this article. Great post sir!
Hehehe... Sir i am flattered. Thanks for turning up!
You are welcome sir.
Of a Truth you have greatly enlightened us on machining.
I applaud your contributions
Thank you for stopping by.
Thank you @adetola for your article. I have been using TiN tipped drills for some time and find them lasting a long time. However, I remember reading that Cobalt drills are meant to be one of the best for drilling steel. Do you have any thoughts on this?
Hello Terry,
Like i said earlier the best tool is not the hardest tool neither is it the softest rather the tool that does your work efficiently at the lowest possible cost. For this reason there is no best tool out there..
I hope this solved your question. Thanks for stopping by.
Thank you @adetola . btw It's cool that you have access to a machine shop, is this part of your work?
Yeah.. I supervise whats going on there. And my boss doesn't mind me taking pictures. I am just a volunteer there to gain more experience
Another great input from you. This is indeed a nice sequel to your previous post.
The HSS tool was the one we used almost all the time I worked at the machining workshop. Its hardness and suitability with cutting different material well made it the best chose.
Well done.. I enjoyed it.
If it was then it probably performed most operations efficiently. That's why you didn't change it.
Oh, true tho.
Nice work. You didn't even have to download pictures to back your post up.
Nice Post sir.
Yea thanks a lot
The way a tool is grinded has an effect on the finishing it gives on the work piece that is being machined.
Very detailed article sir. 👍
Yea that's true.. Thanks for stopping by.
That was quite exhaustive....... those little lights emmited in the process of shaping hope they don't burn😀, just been curious.
I see it a lot especially when welders are working
Hehehe they do not burn and as long as you do not have combustible fluids on your clothes you are safe.. I used to be scared of it initially. But now i am not anymore. Thanks for being here.