Drill bits The first contact in the extraction of oil
Make a hole through a wick that cuts and crosses the strata of the earth's crust. We can compare it to the procedure of opening a hole in the wood, for which the drill is used, as is well known. In fact, when we want to open a hole in the wood we apply the tip of the drill bit to the place where we want to drill, then we press while we print a rotary movement and in this way penetrates the wick. Drilling wells are something similar. By the rotary method a wick is made to rotate at the lower end of the perforation pipe, the upper end, joined to a tube of square section, is introduced into the rotary table where it is strongly grasped by two clamps. its action the trephine rotates at an adjustable speed that can reach more than 150 revolutions per minute, with which the perforating action acquires great effectiveness.Each time they have drilled 9 meters (length of a drill pipe), a new tube and the operation is continued.
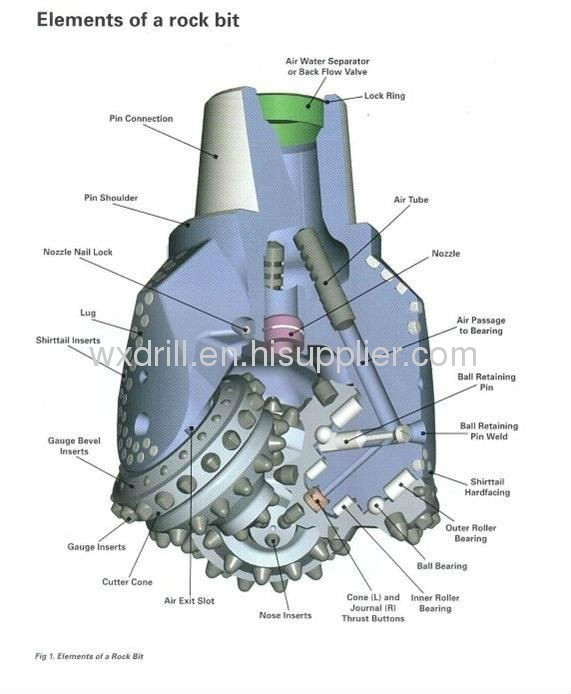
The Choice of the drilling bits
The type of wick in use must adapt to the geological conditions of the place where you work. Some have at their end two blades in the form of fins with smooth edges (fishtail), other types have serrated edges and there are also with certain rotating parts as in gear (strawberry wick). For very hard strata it is possible to use trephines with the tip of industrial diamonds and for the extraction of nuclei of the land, they are used augers. The speed of the drilling fluctuates between a few meters and hundreds of meters per day, depending on the resistance of the rocks. It is very frequently the wear of the wick by friction effects, in which case it is necessary to extract all the shank pipe, uncouple it and pile it inside the tower; once the wick is changed, the pipe is collected, it is coupled and it is lowered into the pit again.
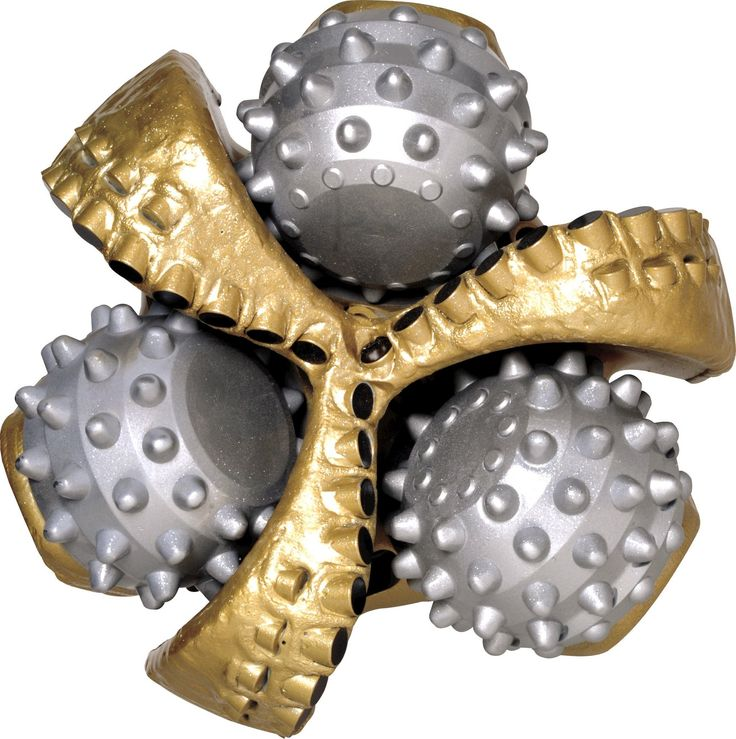
THE START OF PERFORATION
The perforation is performed by means of the rotating action of a cutting steel wick tightly bolted to the lower end of an axis formed by steel tubes, whose length increases as the well or hole is deepened, adding new pipes to the upper end of the shaft or pipe. The task of adding or subtracting pipes from the shaft or pipe, or removing or inserting it into the hole, as circumstances require, is therefore fundamental and constant work in drilling, and for this it requires a point of support in the space, at sufficient height, that allows us to raise or lower the drill pipes in sections of up to 27 and more meters. This point of support in space is provided by the derrick, which we will see that it also has other functions. We must also have a power plant and the mechanism required to print to the pipe and the wick the rotary movement necessary to drill the rock layers, and also with the pumps and the mechanism of cleaning and conditioning of the well, made to measure that the drilling progresses.
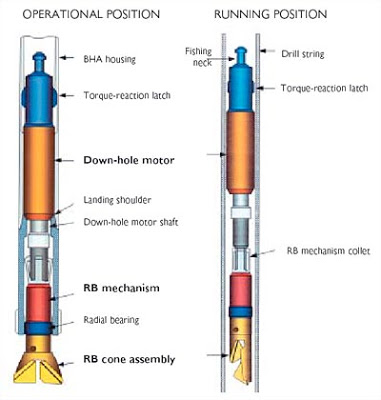
POLYCRYSTALLINE AND DIAMOND BITS
These bits have a long life because their cutters are very hard and there are no bearings or moving parts.
The industrial diamonds of natural origin used are manually placed in geometric designs that cover the bottom of the bit, in a redundant way that allows the operation of the same if there is a break of any of them. In PDC drills, polycrystalline diamonds are mounted in a matrix of tungsten carbide. Diamonds perform drilling or cutting, while tungsten carbide supports them by providing them with strength and rigidity. Diamond cutters start their work sharp and wear out while staying sharp, while most cutters wear out with use. This and its long life make it extremely cost effective for deep drilling and hard and abrasive formations. Since they do not have moving parts, they are economical and allow high rotational speeds (RPM), (higher than those allowed for drill bits) produced with backup motors. They have a long life, although the penetration rats (ROP) are generally smaller. The perforated distance will have to be greater to justify the high cost involved in these bits. The cutting action of the diamonds is of the type of fault or spray. Which produces cuts that are much finer than those produced by a tricone drill.
Commonly appearing as a fine rock meal, and sometimes even thermally altered due to the high frictional heat generated. This makes this bit not very useful when it comes to evaluating a formation, because the structure and shape of lithology are destroyed to a high degree. Similarly, they are not sensitive to changes in formation (usually a change in the ROP is the first indication of a change in lithology), it is emphasized again that these drill bits do not produce cuts suitable for geological evaluation. Diamond drill bits have different operational requirements than tricone bits. They generally have a diameter slightly smaller than the hole size to reduce wear during in-and-out trips.
Optimum performance is achieved with low WOB and the highest possible RPM, and with high mud speeds around the cutting surfaces of the bit. Before starting to drill with a new drill of these, it must be 'seated', in other words the shape of the hole in the bottom must be adjusted slowly with the drill bit; this is achieved by slowly increasing the weight on the bit (WOB) before starting to drill, so the profile of the bit will slowly give its shape to the bottom of the well.
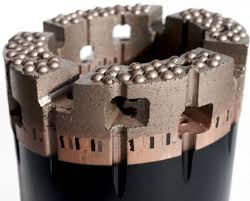
Being A SteemStem Member
Thanks for the support of the steemstem group