A BETTER APPROACH TO PROBLEM SOLVING
Overview
Total Quality Management (TQM) is an integrated effort designed to improve quality performance at every level of the organization. It is about meeting quality criteria as defined by customer which could either be conformance to specification, fitness for use, value of price paid, support services or psychological criteria. In the semiconductor industry where I belong, we ensure that our product meets or exceeds customer requirements such as dimension, appearance and electrical characteristics hence conformance to specification. TQM as a philosophy has the following core concepts;
- Continuous improvement (Kaizen)
- Customer focus
- Employee empowerment
- Use of quality tools
- Product design
- Process management
- Managing supplier quality
I will be elaborating on the concept of continuous improvement and promote a more effective approach to problem solving
Continuous Improvement (Kaizen)
Kaizen is the Japanese word for “improvement”. In the industry, it pertains to continual improvement initiatives for every aspect of the business and empowering all members to contribute from President down to line operators. Kaizen focuses on small yet consistent improvement through consolidated efforts from all members.In the context of manufacturing, process and product performance is continuously evaluated to identify problem points and take actions to improve it. W. Edwards Deming reported that 85% of quality problems are caused by process and systematic errors, and poor management while only 15% is due to worker’s error. Deming as the “father of quality control” conceptualized the Plan-Do-Study-Act (PDSA) cycle commonly known as Deming cycle. Its cyclic nature perfectly embodies the kaizen philosophy, the never-ending improvement.
You might be wondering, isn’t it PDCA and not PDSA?
PDSA evolved from Plan-Do-Check-Act (PDCA), but why is this so? To clarify, let’s differentiate “check” from “study”. Check is more on the comparison between current and expected performance or function. Study on the other hand, goes beyond comparing for it gives emphasis in using the comparison data to further understand the process or product to be improved and predict its trend or behavior.
What is PDSA?
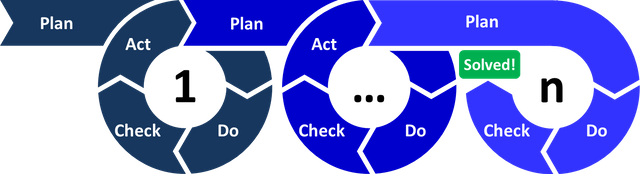
PDSA is an iterative methodology for process or product improvement. It consist of the following four stage;
1. Plan- Define the problem
- Formulate hypotheses
- Set improvement criteria
- Develop prototype
- Conduct experiment and test hypotheses
- Select and propose optimum alteration
- Gather and interpret results
- Implement alteration on a larger scale (pre-production)
- Judge results based on improvement criteria. Fail – go back to “plan” and try again. Pass – proceed to 4th stage.
- Implement recommended improvement (mass production)
- Assess impact and standardize alteration
- Update and re-rank remaining defect modes based on its contribution
DMAIC – New and more effective approach to problem solving
DMAIC, or define, measure, analyze, improve and control is not entirely different from PDSA approach. Both techniques shares the same objective however, DMAIC places profound emphasis on data and preparation.
Do and study are lump into improve stage of DMAIC. It starts with smaller scale (prototype) evaluation and then larger scale (pre-production) evaluation to assess the realistic over-all impact of the alteration. This reduces the risk of decision-making and yield attainment projection errors.
Finally, act stage is similar to control stage. It focuses on implementation and realization of the recommended process or product improvement. It covers standardization of alteration and necessary controls i.e. check sheets, SPC, etc. to ensure correct implementation and sustain impact.
PDSA or DMAIC? Which do I prefer?
I strongly recommend DMAIC approach. Why?
- Professionals especially those industry novice are full of ideas, we tend to struggle in organizing our thoughts. DMAIC can maximize our critical thinking skills by putting ideas in right places and analyzing problems methodically.
- DMAIC is data driven. Not all professionals are fluent in the English language but all of them are ought to comprehend graphs, trends and statistics which are derived from data acquired. I consider data as a universal language particularly for engineering professionals. If there is a language barrier, let your data do the talking. However, a good communication skill is a huge advantage.
Practice makes perfect. Start applying DMAIC in your problem solving endeavors and be consistent with it. A rewarding professional career shall come after.
References
Text reference
1. Shankar, R. (2009). Process Improvement Using Six Sigma A DMAIC guide. Milwaukee, Wisconsin: ASQ Quality Press.
2. Wiley Contributors. (n.d.). Total Quality Management Chapter 5. Retrieved 2 7, 2018, from https://www.wiley.com/college/sc/reid/chap5.pdf
Image reference
1. Daily News Ph. (n.d.). Thinking Pinoy Finally Revealed His Identity. Retrieved 2 7, 2018, from http://www.dailynewsph.com/2017/01/watch-thinking-pinoy-finally-revealed.html
2. Trestles Construction Solutions. (n.d.). The DMAIC Cycle - 5 Phases of Lean Six Sigma. Retrieved 2 7, 2018, from https://trestlessolutions.blog/dmaic-5-phases-of-lean-six-sigma/
3. Wikiwand. (n.d.). PDCA. Retrieved 2 7, 2018, from http://www.wikiwand.com/en/PDCA
thank you for this helpful post @ jeebee0331
I'm glad to be of help to you
As an IE, I prefer DMAIC process too.
wise choice