It’s nice to be proven correct every so often
It’s nice to be proven correct every so often
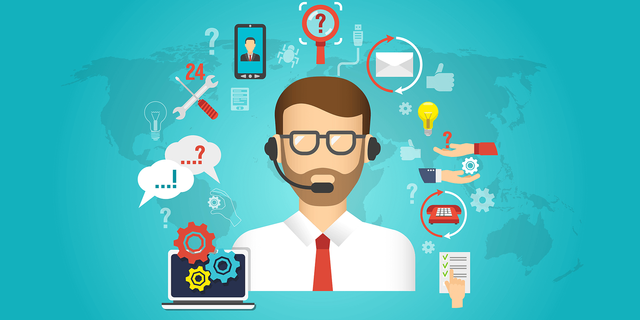
I work with a bunch of different different types of analysers and control panels. I have a customer with a simple-to-use panel that triggered a relay in the event of specific alarms.
He’d asked if I could update the configuration on it to had some additional alarm events to trigger that relay. So I did that for him during a routine service visit.
Unfortunately, due to the industries I generally work in, I learned to work on the equipment that I’m there to work on, and trained to work on. I’m here to work on that specific box on the wall and the specific equipment connected to it. I’m not going to touch anything outside of that.
So sometimes I can feel like a bit of an asshole for refusing to work on other equipment on a site. I might any questions or point the customers in what I think is the right direction but making sure to completely cover my ass the whole time.
So I have the customer’s control panel reconfigured and confirmed that it’s doing what it’s supposed to be doing when the various alarms happen, and aren’t happening. All looks good.
A week or so later I get an email from the customer saying that my control panel isn’t working properly. I happened to have a scheduled visit for routine work the following week and asked the chanter if it’d be OK if I looked into it then. They were fine with that.
Routine service visit goes fine and I do my testing on the control panel. It’s doing what it’s supposed to do. I note this in my report.
A few weeks later the customer asked me to come back to site to review an installation by another company, and while there if I could look at that other control panel because it “still isn’t working right”. No problem.
My review of the installation goes as expected and I test the control panel again. It’s working fine. I note this in my report.
The customer is getting a little frustrated because I’m telling him that my panel is working fine, but another contractor is insisting that he isn’t seeing the “signal” (a switch closing) from my panel, and that there must be a problem with my panel.
Another site visit is arranged where the other contractor and I will be on site together to sort it out.
We meet, he seems alright, but overly cockly that the problem is on my end if things, so I suggest we start there. We go to my panel and I ask him what he expecting to see. “An open contact in normal conditions, a closed contact in alarm conditions”. Perfect.
I show the other contractor the relay, take out my multimeter and test the relay with the system in normal condition, as expected the contact is open. I simulate the alarm conditions, we can here the relay click, the LED on it has turned on, showing that it has been energised and I test it with my multimeter. It’s now a closed contact.
But we don’t hear the audible alarm that is supposed to be triggered on his end. I ask him if he’d just to test the relay with his gear. He doesn’t.
So we start going through the rest of the circuit by this stage I know I’m good,nice known if for weeks but I want to see where the issue was.
The other contractor checks an IO panel that’s part of his setup, where it’s supposed to see the closed contact from my panel. We simulate an alarm again, my panel triggers the relays, his IO doesn’t see it. He tests the wires coming into his IO panel with his equipment and confirms it’s a closed contact, and then notices the problem his IO panel is wired incorrectly. He looks just a little sheepish. I smile.
He does to his work vehicle, gets the things he needs (it was a 90 second fix), and I trigger the relay in my panel again. His IO sees that, his main panel the IO is connected to sees it and the audible alarm sounds, and all is right in the world again.
I made sure to note all that in my report too!
That was the start of my day, which happened to be a Friday and the rest of the day went well. Nice way to start the weekend.## TLDR Summary: