Audio Newbie #2: Vinyl Records Suck! Really?
Introduction
There's nothing better than spending cold winter evening at home in your comfortable armchair set near to good-looking fireplace with glass of good red wine or expensive, old whiskey and music... Music played from oldschool vinyl recording which you bought on internet auction because everyone says there's nothing better than warm sound of music played from analog disc... But is it true? Are vinyl recordings as good as they say? Maybe it's only a myth? Let's check this out!
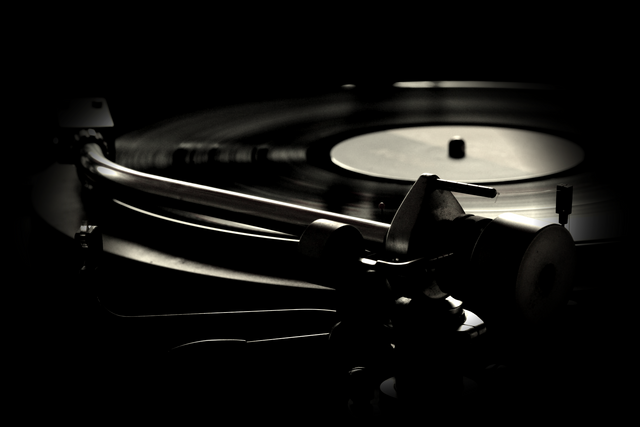
Part of History of Sound Recording
The acoustic era of sound recording started in 1877 and ended in 1925. The first practical recording technologies were fully mechanical. They usually had huge horn to collect the sound and they also had an articulated scriber or stylus which under the pressure of air, produced by for example singing, was scratching a metal cylinder coated with wax. Sound quality of those recordings was awful to be honest and they had frequency response from around 250 up to about 2500 Hz.
The second wave of sound - the electrical era started in 1925 and ended in 1945, it's worth to mention the fact that in this era they have started adding audio to video. This era started by introduction of Western Electric's integrated system of electrical microphones, electronic signal amplifiers and electromechanical recorders which were adopted by US record labels in 1925. This era gave us possibilities to capture, amplify, filter, balance electronically the sound, it also gave us much wider frequency response - from 60 Hz to 6000 Hz. It basically means that audio engineers were able to capture fuller, more detailed and balanced sound on record using multiple microphones connected to multi-channel electronic amlifiers, compressors, filters and mixers.
Creation of Vinyl Records
Have you ever wondered how they made vinyl records? Yes? That's great! I'm happy you are very curious person and you're willing to learn new stuff everyday. No? Then just skip this point.
Master discs are made from aluminum core, which is sanded down to smooth finish. Then they coat them in a nitrocellulose lacquer. Once dry, nitro becomes a thick coating similar to nail polish. Before they go to the next step of the creation, master discs must be checked for any bruises and bad stuff like that. When inspection is done, they carefully pack new discs in batches using separation strips between each other to avoid damaging the lacquer surface.
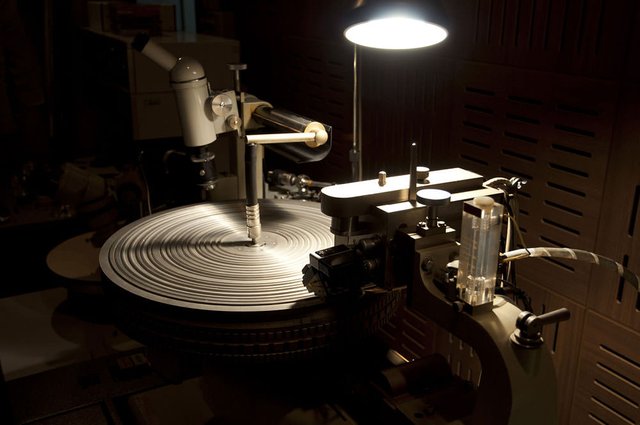
Master discs are sent to studios where engineers place them to lathes. This is the process of recording, they use lathe to cut a continous groove representing the source material using a sapphire tipped cutter. Whole process is monitored via a computer which is responsible for ajusting the spacing between grooves if required. In the past, engineers had to do it manually, this is why they were using special matrixes to count how many lines of groove fits into them. To be honest, They had really responsible job because one small mistake could lead to making whole recording sound bad.
Now, we want to create vinyl records from the master records, so we have to create a stamper. This process begins by washing the master disc and then spraying it with tin chloride and liquid silver. Any silver that doesn't stick is washed away. They add a duller material to the silver side, which stiffens the disc ready for the electroplating process.
And what is electroplating? It's the process that involves immersing the silver plated disc into a liquid tank of dissolved nickel. When immersed, the nickel is fused to the silver surface by an electrical charge. When the nickel is set into the grooves, they remove the disc from the electroplating tank and they remove the metal layer from the original lacquer disc.
Before pressing the records, they prepare the labels which are created in square stacks and then then punched in the center and trimmed into circles. Finally, we can start talking about pressing vinyl records. To do it, they have to pour polyvinyl chloride pellets into a hopper which feeds the material into an extruder that condenses them into a small puck shape reffered to as a biscuit. Those biscuits and labels are then moved to the press where 100 tons of pressure is applied to them at very high temperatures to melt and mold the biscuit into a new vinyl record.
Real Sound of Vinyl Records
NAB (RIAA), TELDEC/DIN
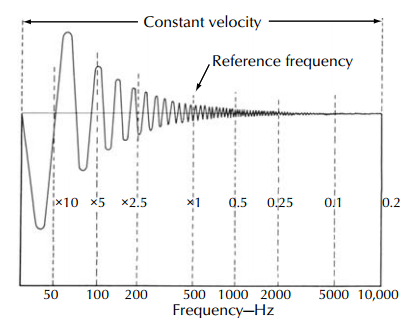
We can see that the amplitude is the highest at low end and the lowest at high end. The relationship between the frequency of the signal and its amplitude where amplitude is inversely proportional to frequency is called a constant velocity characteristics. If audio was recorded without NAB (RIAA) or TELDEC/DIN equalization, low frequencies would take all of the space and high frequencies would be of such a low amplitude that they would be very close to the noise level of the system.
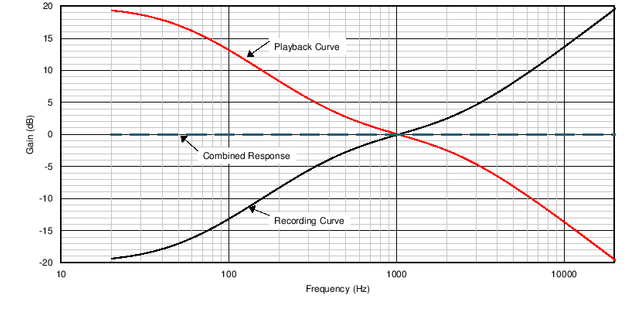
Preemphasis (recording curve) - the equalization used for cutting.
Postemphasis (playback curve) - the equalization used in playback equipment.
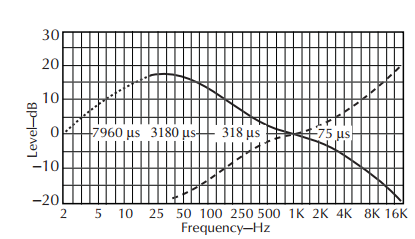
Let's take a look what happens here in case of RIAA curve:
Frequency (Hz) | Recording Characteristics (dB) |
---|---|
The NAB (RIAA) curve covers the range from 20 Hz to 20 kHz and the TELDEC/DIN curve extends the control over playback down to 2Hz where equalization returns back to 0 dB. Unfortunately, devices and vinyl records applied with TELDEC/DIN curve aren't as popular as those with NAB (RIAA) curve.
Vinyls For DJs
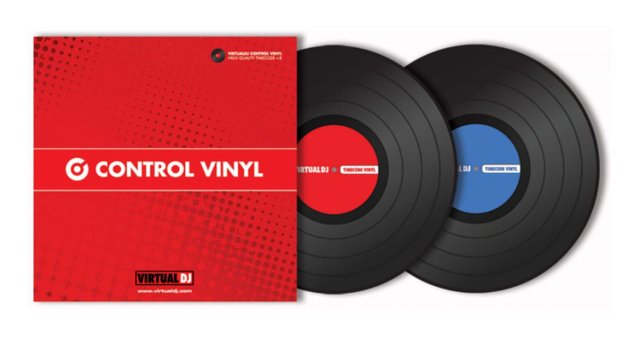
DVS or Digital Vinyl systems allows DJs to use software like Traktor, Serato or Virtual DJ and digital music (.wav, .mp3, etc.) with turntables.
Advantages of this solution:
- You don't need to buy a lot of vinyl records.
- You can practice mixing in oldschool way in your own bedroom.
Disadvantages:
- You will need DVS enabled controller, audio interface or mixer.
- You will have to replace them for new set one day because they wear out.
- You have to clean them from time to time.
Summary
What you can hear while listening to music from your vinyl record is the sound of amplifier with applied NAB (RIAA) or TELDEC/DIN curve to it, not the sound recorded to your vinyl record. You also should be aware what causes all of those noises and crackles that you can hear while listening to your record. Those unwanted sounds are created due to needle going through dust or small bruises.
I'm not huge fan of vinyl records, but I like them for 2 reasons, which are:
- They are the only analog audio storage that we have these days.
- It's funny to see that disbelief in eyes of vinyl records' fanboys when you tell them what are curves like NAB (RIAA), how they are used and what they really hear.
What I can agree to, is the fact that person who revived vinyl records is a genius and she or he should get a huge prize because it is really amazing idea to play with people's feelings by reminding them old, good times of their youth, right?
Additional Knowledge for Geeks:
Record Diameter
12 inch LP disc, 33 1/3 rpm - 11.875 ± 0.031 inch (301.6 ± 0.8 mm)
10 inch disc, 33 1/3 rpm - 9.875 ± 0.031 inch (250.8 ± 0.8 mm)
7 inch disc, 45 rpm disc - 6.875 ± 0.031 inch (174.6 ± 0.8 mm)
The recorded surface should start with at least one turn of unmodulated groove.
Maximum Outer Diameter
The maximum outer diameter of the recorded surface should be:
12 inch LP disc, 33 1/3 rpm - 11.500 inch (292.1 mm)
10 inch disc, 33 1/3 rpm - 9.500 inch (241.3 mm)
7 inch disc, 45 rpm disc - 6.625 inch (168.3 mm)
Groove Dimensions
The groove dimensions should be:
Minimum top width (monophonic only) - 0.0022 inch (0.56 mm)
Maximum bottom radius - 0.00025 inch (0.006 mm)
Included angle - 90° ± 5°
On stereophonic records, the instantaneous groove width shouldn't be less than 0.001 inch (0.025 mm). The average groove width shouldn't be less than 0.0014 inch (0.035 mm).
Finishing Groove
The diameter of finishing groove should be:
12 inch and 10 inch discs - 4.187 ± 0.31 in (106.4 ± 0.8 mm)
7 inch discs - 3.875 ± 0.078 in (98.4 ± 2 mm)
That was very interesting! - I never tought much about how vinyl records are made - but i love the crackling sound - when i listen to vinyl records it's always a bit sentimental ;) .
I love my vinyls , not so much for quality , we can get higher quality digital files nowadays (at least higher quality than the vinyls recordings I can afford) , what makes me really love that medium is that I am forced to actually stop and listen the album.
It makes harder to change songs or switch albums making me more likely to listen the full album and actually enjoy the song instead of going like "Oh that riff just made me remember that other band , what was that song? lemme search, oh right that one , let me listen... oh look that record label did that other album , I must listen that song"
Actually, this is very good thing. I've noticed that I have problems with listening whole album in digital format because I like to skipping parts of song which seems boring to me... Anyway, I'm way too lazy to change a vinyl record for the next one when the previous one ends, it takes too much time.
Basically vinyls are the final solution against Music ADHD.
Very interesting information. Thanks for sharing.
Resteemed!
This color flower is very much like me