Material damage caused by voltage #Mechanical Engineering Part I
Greetings.
How are you Steemit friends? Wish you good health always.
Today I will discuss the material about the problem that happened to a material or iron that is Fatigue.
We Can Know, Fatigue Not just happen to humans, Fatigue can happen anywhere. Let's Learn together from some of the most trusted sources I discuss below.
In materials science based on references from Wikipedia.
{here}
Fatigue is the weakening of a material caused by the burden which is repeatedly applied to the material causing progressive structural damage and a cyclically charged material.
After the weakening of a material, the nominal value of the maximum stress that causes damage as the final limit of tensile strength loading, or the limit of the yield stress.
In general, I can explain that the surface of the material will provide a limit of endurance, the effect of changes on the surface of the material is very decisive from the material structure. Fatigue occurring in the material can be caused by the arising of crissal formation cracks, this is due to the magnitude of the maximum voltage of the material is not proportional to the load it receives.
We can know the fracture mechanism is generally started from the surface of the weak material, which then will propagate to the middle and eventually the material will experience a fracture. The fracture may occur suddenly with little or no plastic deformation.
Fatigue in the material can be tested two-step ways of starting cracks and crack propagation until the total crack. The majority of fatigue life occurs when crack exhaustion begins and the fatigue process is described when it is first controlled.
{Advanced discussion of two steps fatigue test}
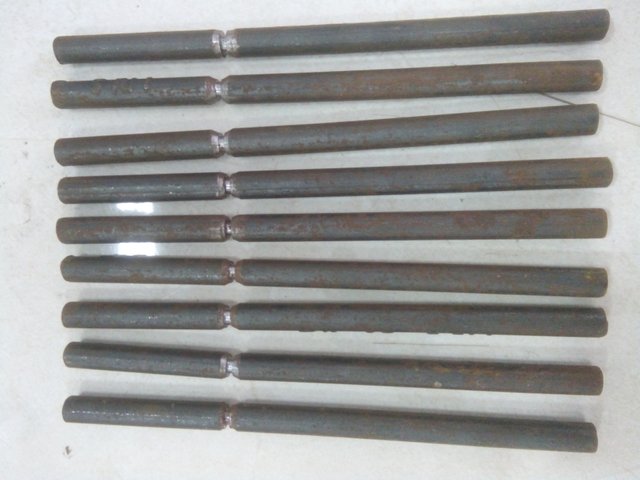
By doing a fatigue test on a material used to determine the fatigue limit of a material, so it can be known how certain load limits where the material is still safe to use or in rely on.
Fatigue tests require accurate control. However, to be good at testing we need accurate control and this can be done with a rotary bending machine.
The work I do
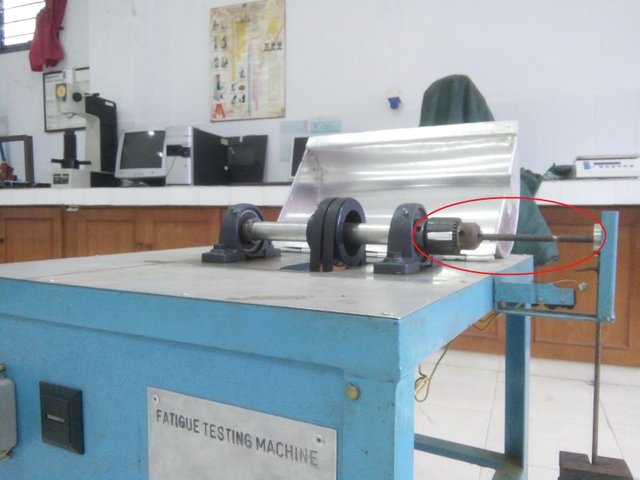
The working step of this machine, a soft, cylindrical specimen loomed and filled from both ends using a spinning mop/leave.
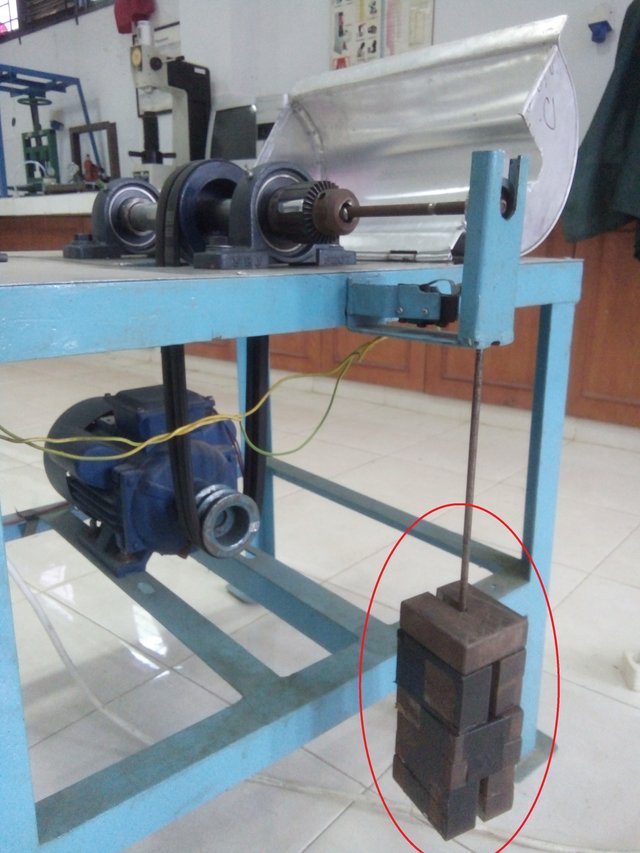
Results
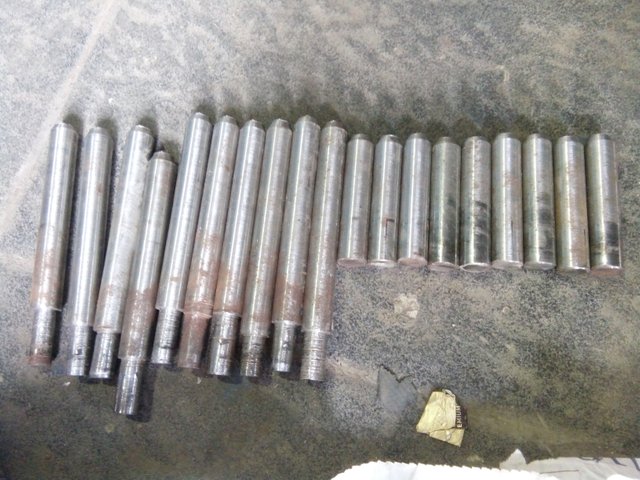
You can watch video from me
One example of research on fatigue test on an ingredient can be seen in the research of a previous study from R. Prochazka, namely the evaluation of fatigue limit of structural materials based on thermographic analysis.
{3rd International Symposium on Fatigue Design and Material Defects, FDMD 2017, 19-22 September 2017, Lecco, Italy}In this study have similarities, where the fatigue limit point is given as the junction of the two regression lines.
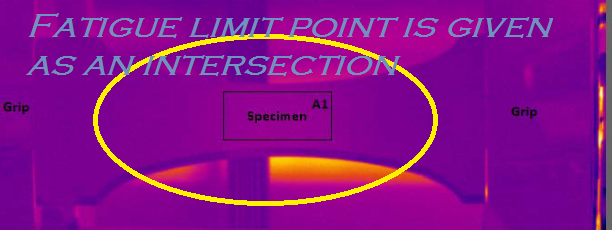
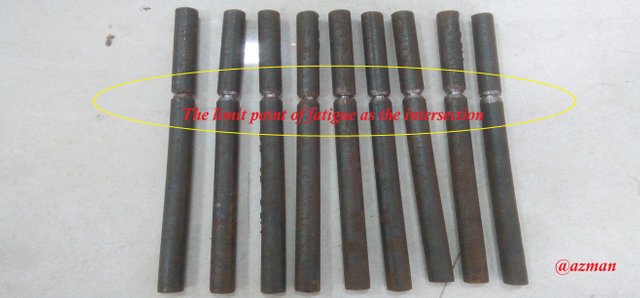
Changes in the material properties of a component can be monitored using non-invasively.
As a first step, the reference fatigue limit based on degraded materials and materials is measured according to the standard.
Influence of Material Changes
The final surface of the section of a material structure is fitted to the tired stress is very important, if the end of the material is not raised according to the standard such as the drawing, the limit of material endurance is not proportional to the load it receives.
You should know 90% of the main causes of usage failure. There are 3 phases in the fracture of material: Cracked start, crack spread, and fracture. The mechanism of the cracking start generally begins with crack initiation that occurs on the surface of the weak material due to repeated loading. Furthermore, is the spread of this crack developing into microcracks. Then after that, the material will experience what is called a fracture. Fracture occurs when the material has undergone a voltage and strain cycle that results in permanent damage to the material.
Conclusion
From the above discussion you can know Fatigue that occurs in the material can be caused by the emergence of crissal crevice cracks, after the weakening of the material it can be seen how a certain load limit where the material is still safe to use or in rely on.
Fatigue testing requires accurate control, the material properties of a component can be monitored using non-invasively.
The cracking mechanism starts generally starting with the initiation of cracks occurring on the surface of the weak material due to repeated loading. There are 3 phases in the fracture of material that is starting to crack, crack spread, and fracture.
Reference
{wikipedia.org}
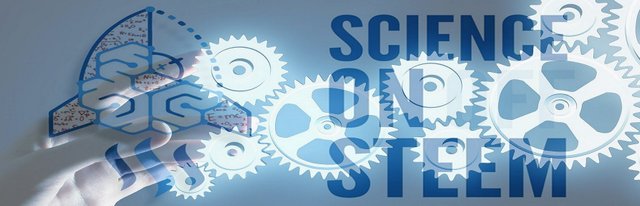
Hello, as a member of @steemdunk you have received a free courtesy boost! Steemdunk is an automated curation platform that is easy to use and built for the community. Join us at https://steemdunk.xyz
Upvote this comment to support the bot and increase your future rewards!
Cool post, thanks.
thank @cmplxty :)
I was always bored by this stuff in collage.