The art of creation: A day in an Engineers Workshop
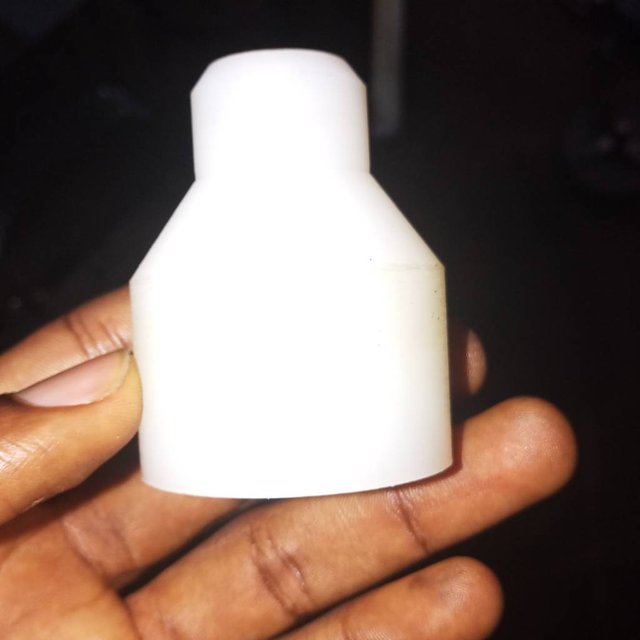
The finished machine part: image taken by me @adetola
“Desperate times calls for desperate measures” this is one quote I would never forget as it was the favorite of one of my feared principals in high school.
But this was the case this morning, as a man walked into my workshop this morning requesting to see my boss (the manager) of the workshop where I worked.
From where I sat, I could see him panic while he was showing a piece of what looked like a machine part to my boss. That could only mean a thing and what it means is that there is a work needed to be done and completed as fast as I can.
Not long after the man left my boss called me up to his office. There I got a drawing which indicates the machine part I must reproduce.
The drawing although was not put to scale but it clearly shows the dimensions and the shape of the machine part to be reproduced.
Let me tell you what this machine part is used for

The machine part in view
If you have wondered how big companies manage to fill up their bottles either for wine or soft drink production. Then you must have concluded that PepsiCo and Coca-Cola do not employ people to hand fill these bottles but rather have machines to do these for them.
These machines that do this refill are called bottling machine and this part drawn or about to be reproduced is the attachment or nozzle of the bottling machine, it is responsible for filling up these bottles.
This machine part is made of PTFE (Polytetrafluoroethylene) popularly called Teflon instead of metal to prevent corrosion and rust as it could be harmful to consumers to find rust in their drinks, therefore, this would be wonderful for the job.
The PTFE used was a white plastic which was machined to give the required outcome.
I would be sharing the step by step procedure and challenge I came across while reproducing these machine part.
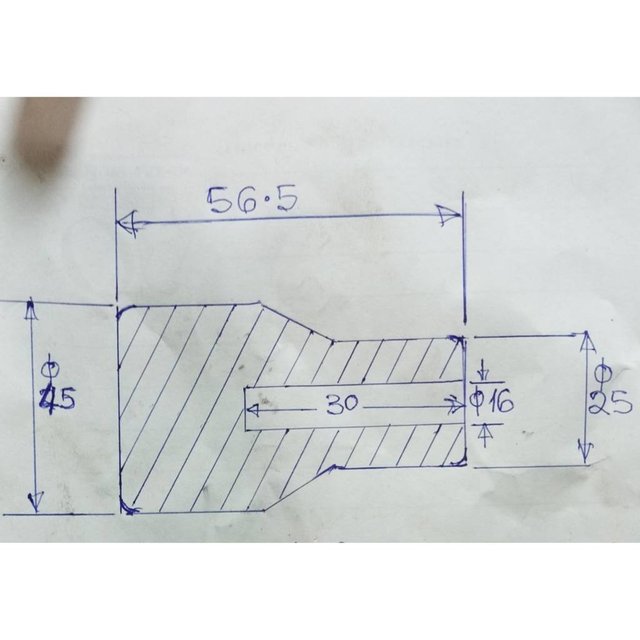
The orthographic projection of the material: image taken by me @adetola

The required tools
The tools used in carrying out this project include the
- raw material (i.e. The Teflon) 50mm in diameter
- A lathe machine
- Cutting tools
- measuring tool in Vernier caliper
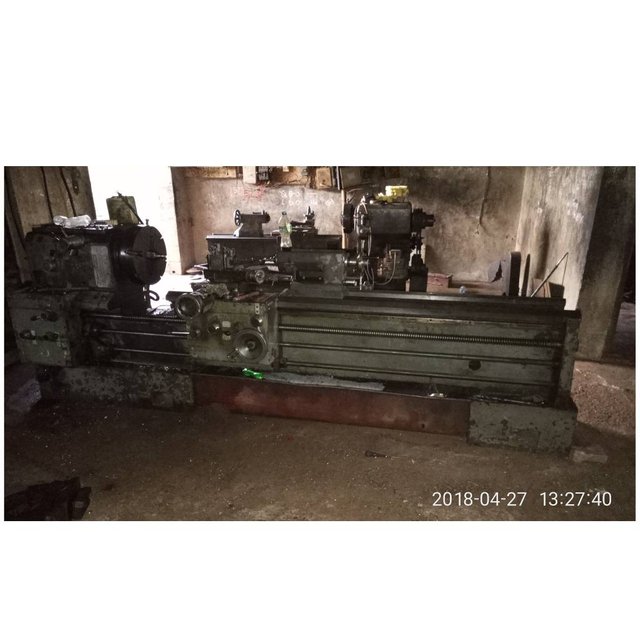
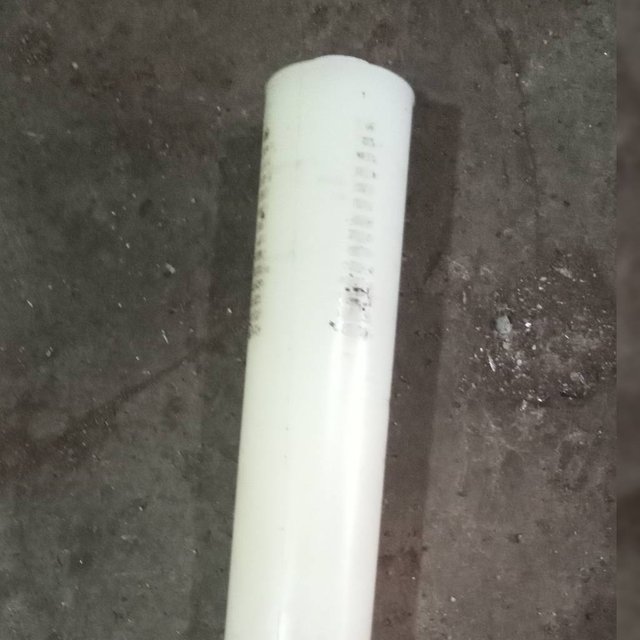
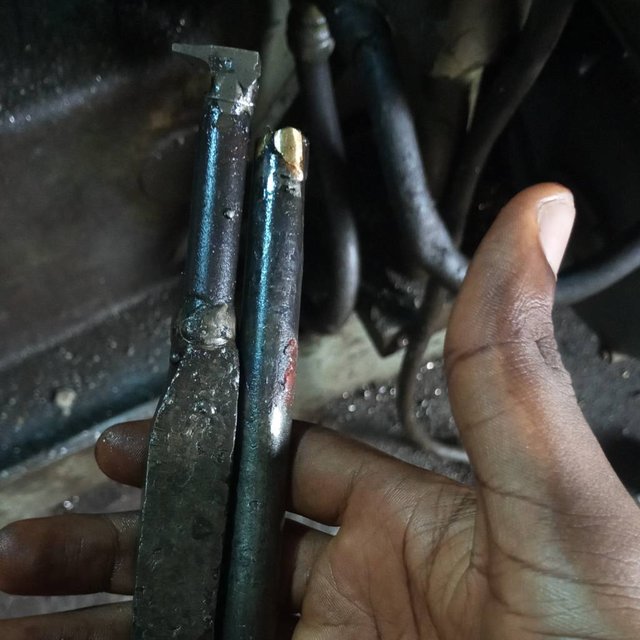
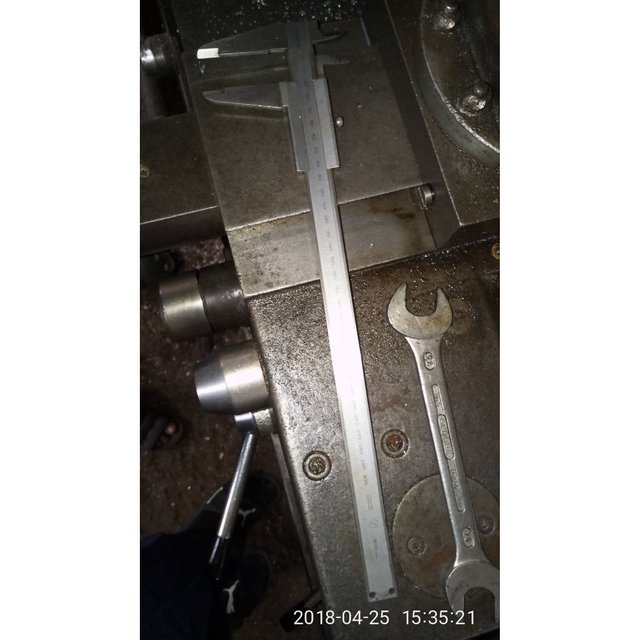

Operation taken to achieve the outcome
The operation began by setting the Teflon in the three jaw chuck that has been set carefully inside the spindle. This requires the machinist to be very careful as a bent work might affect the final product which may result from machining.
This is done using a Guage.
The facing operation
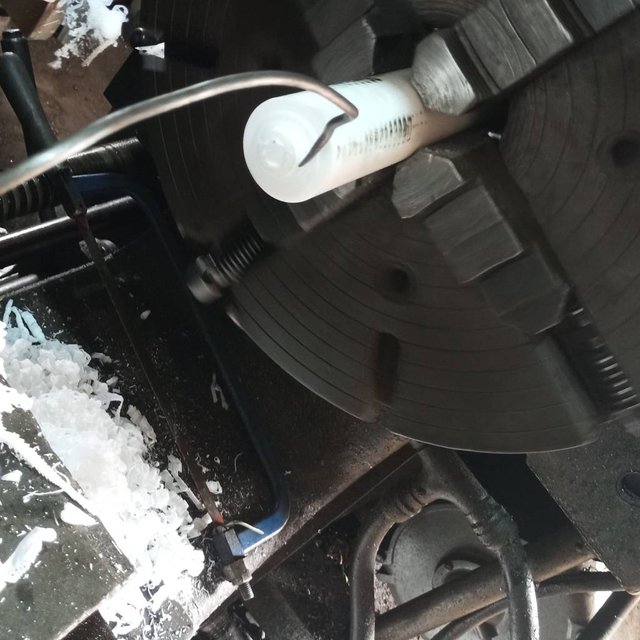
facing operation being carried out: image taken by me @adetola
The first operation carried out on the (50mm diameter) Teflon was the facing operation. And this requires relieving the material of its old surface and giving it a smooth and a new one which is well balanced and suitable for the given work.
The facing operation was carried out using the facing tool (high-speed steel) which is placed on the tool post with the tool post being set at a perpendicular angle (90-degree angle) and fed to the tool rotating at a medium speed.
As the tool meets with the surface of the tool it is being peeled of while it forms a chip (material removed from the job) which is continuous or does not break off easily.
After this is completed the material has a new face with part of its length reduced slightly.
Turning operation
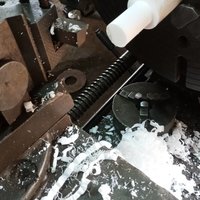
turning operation being carried out: image taken by me @adetola
This is the next operation carried out on the job to get it into shape.
Turning involves the removal of the diameter of the cylindrical surface. This had to be done gradually and in a way that would not stress out the tool. The 50mm diameter was then reduced to the 45 mm diameter for a length of 57mm across the Teflon after repeated to and fro movement of the tool post. The tool is fed in a perpendicular direction to the rotating surface of the tool. You may be thinking just like the facing tool?
Yes, it is just like the facing tool except for the fact that you are not cutting away the surface but reducing the diameter of the job, therefore, you do not allow the tool to go deep into the material.
Step turning
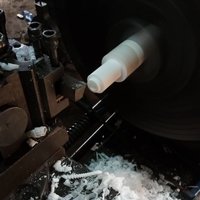
step turning operation being carried out: image taken by me @adetola
A step turning operation is an act of creation because it is like constructing a step on a cylindrical surface. Such that you move from a place of lower diameter to a higher diameter. Just like a real step which has a raiser, this one you are creating to will have a raiser and this raiser is formed by reducing a specific part of the diameter of the job to a certain diameter such that it now has low on one end and a higher diameter at the other.
This is done just like the facing operation just that one part is repeatedly machined to a certain diameter of 25mm diameter while the other remains at 45mm diameter for a length of 20mm across the total length of 57mm of the facing done earlier.
Tapering operation
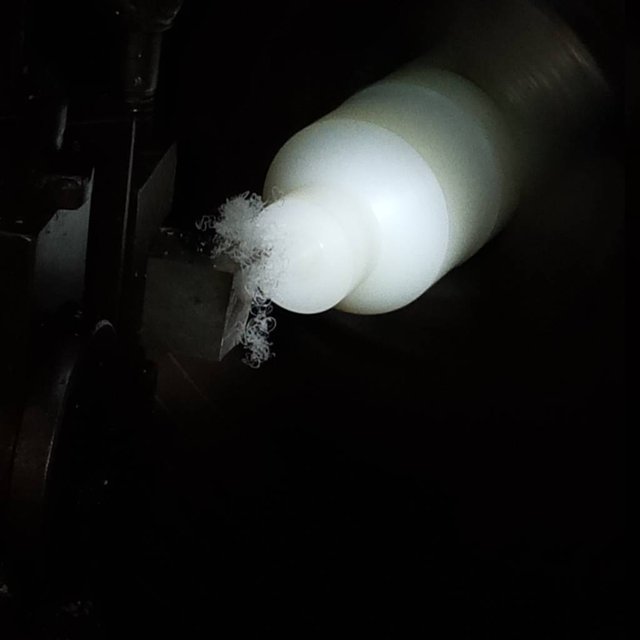
tapering operation being carried out: image taken by me @adetola
If you look at the drawing of the job compared to what we have produced with the lathe machine we have a slant edge. This slant edge is as a result of taking the raiser down at an angle and what it means that the tool post has to be set to an angle that is parallel to the horizontal plane.
This is done with a little mathematics of which we both are going to do together. First, we have to make use of our vernier calipers to take measurements of both the big diameter (D) of the step and the small diameter (d) also we have to take the length (L) across which we want the slant edge to spread across. after taking them we are going to put them in this formula for taper turning.
The tool post is then set at an angle calculated to be 24 degrees. It is just like forming a cone on the step so there is no edge anymore for the step.
Note each measurement is done carefully to monitor and ensure that the material formed is precise else it wouldn't be useful for the actual job it is required.
Drilling operation
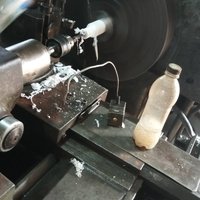
drilling operation being carried out: image taken by me @adetola
On the tiny edge of the cylinder which we have formed I mean the edge of the cylinder with diameter 25 mm. According to the drawing, there is a hole (16 mm diameter) which was drilled inside the material.
The 16 mm diameter drill was therefore fixed in the tailstock of the lathe and fed carefully to the material to a length of 30mm depth inside the job. It was ensured that the hole fell at the center of the Teflon to ensure neatness of the job.
The chamfering operation
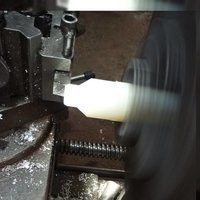
chamfering operation being carried out: image taken by me @adetola
This is almost the last step of the production you might not see it in the drawing but in engineering, we care about safety and this operation is more of a safe way for people to handle this material and make it sit perfectly where it is being used.
It involves removing all the sharp edges made during the production of the part. So, it's smooth and soothing to touch.
Don't forget all these measurements were possible due to the usage of the Vernier caliper which is more accurate than just any ruler.
The cutting operation
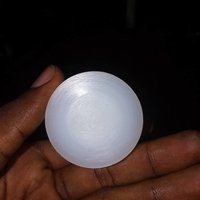
piece after being cut: image taken by me @adetola
I put this together because they are the last operation of this machine part production.
If you remember our raw Teflon material which we are reshaping it is very much longer than the machine part we are trying to form out of it, therefore, we need to cut it.
Cutting on a lathe might be tricky I stated above that we used a length longer than the one in the drawing for this reason just in case your hands are not straight like mine.
But there is an easy way, you remember the step turning operation? You can always go back to it.
This way could be used to ensure that the cut you are about to make is straight. You fed the material the tool at a concentrated point where you intend to cut when the cut has been made deep then it could be traced and done with the hacksaw. This way your cut is always straight.

Image gallery
You would see some images and a video in my gallery about how these operations are carried out on these materials.
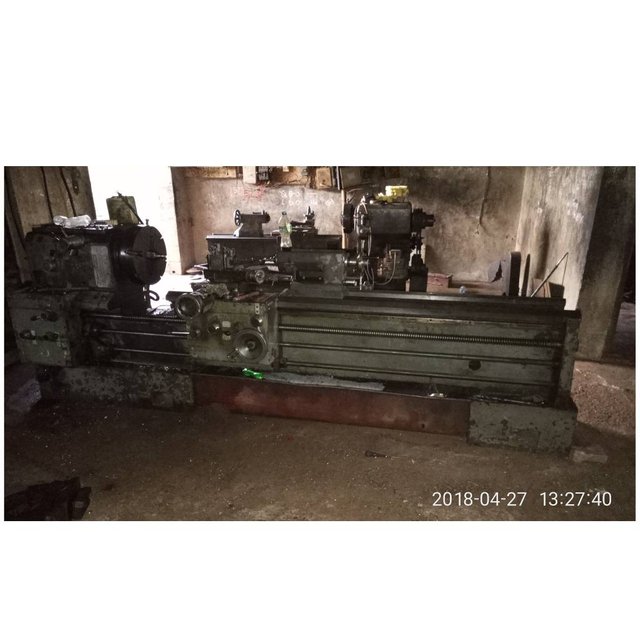
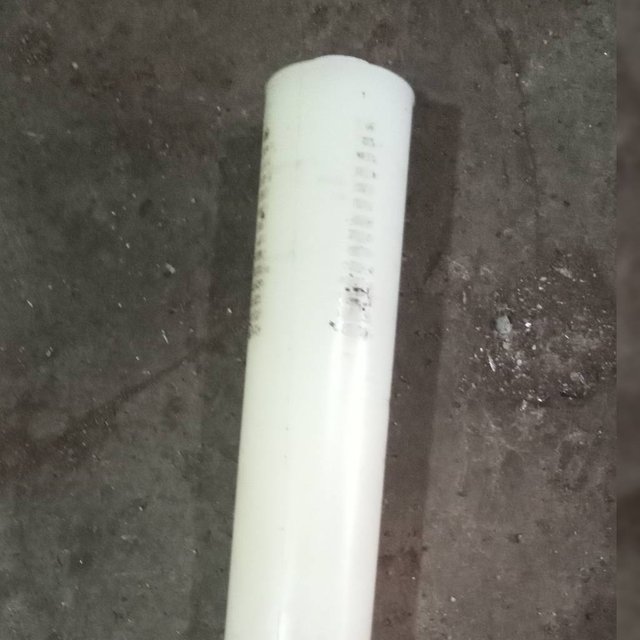
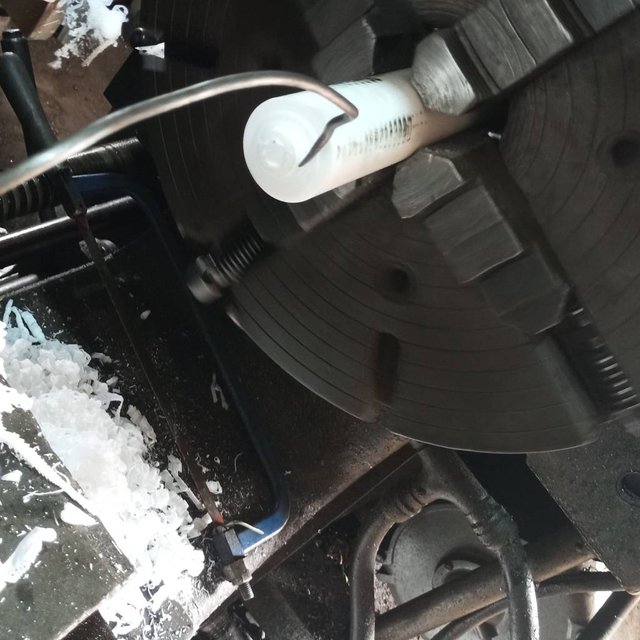
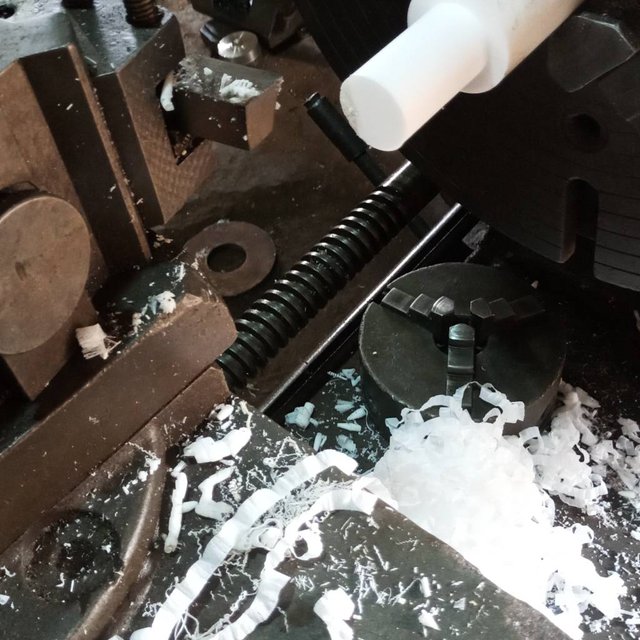
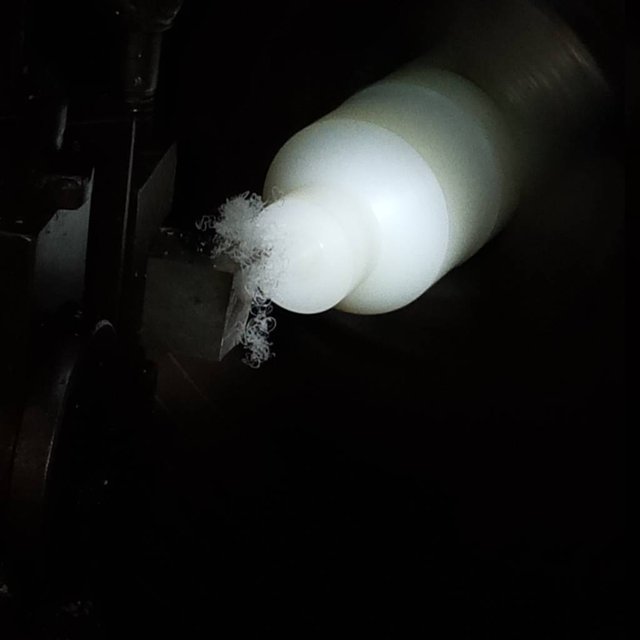
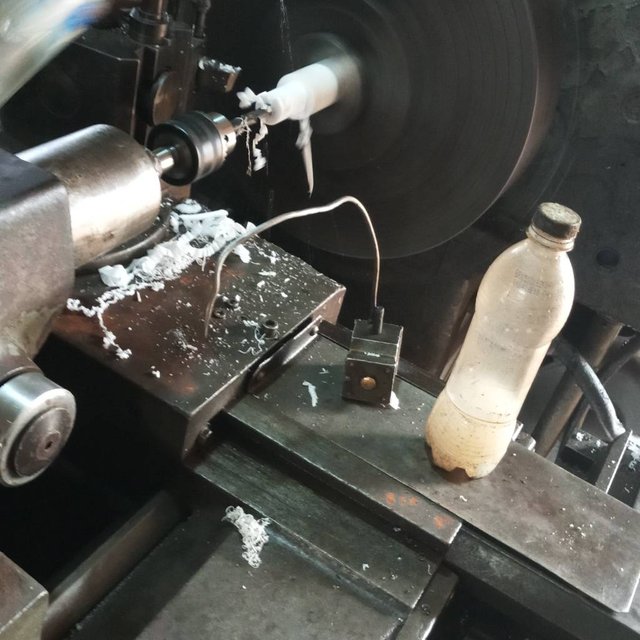
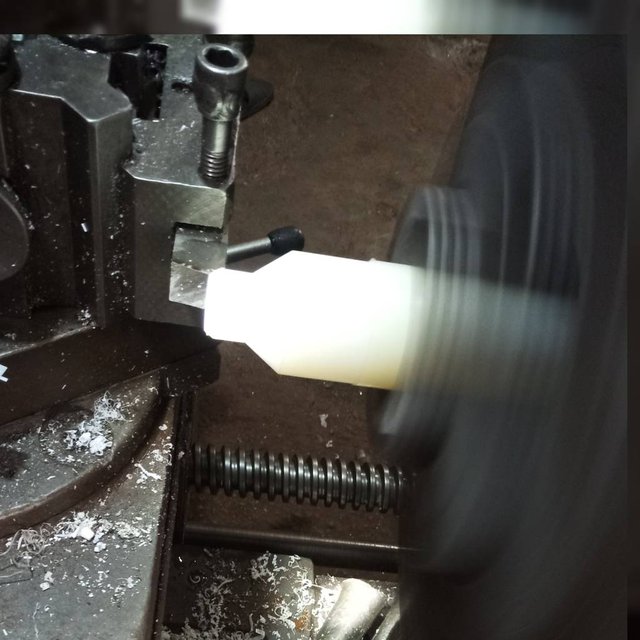
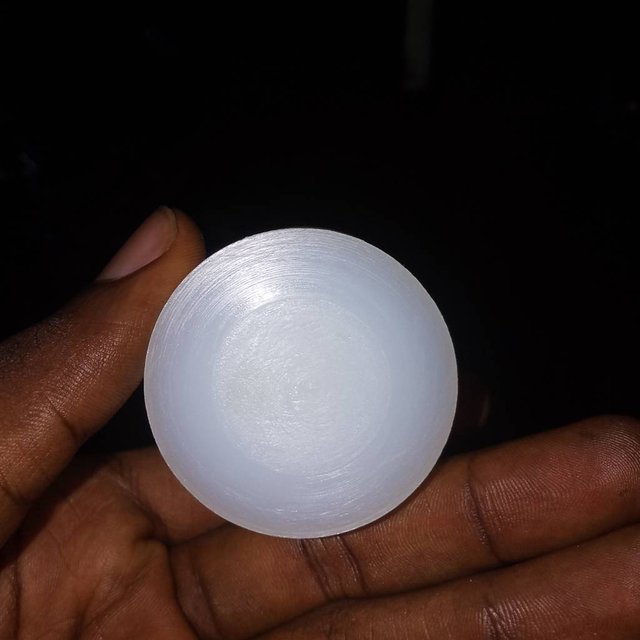
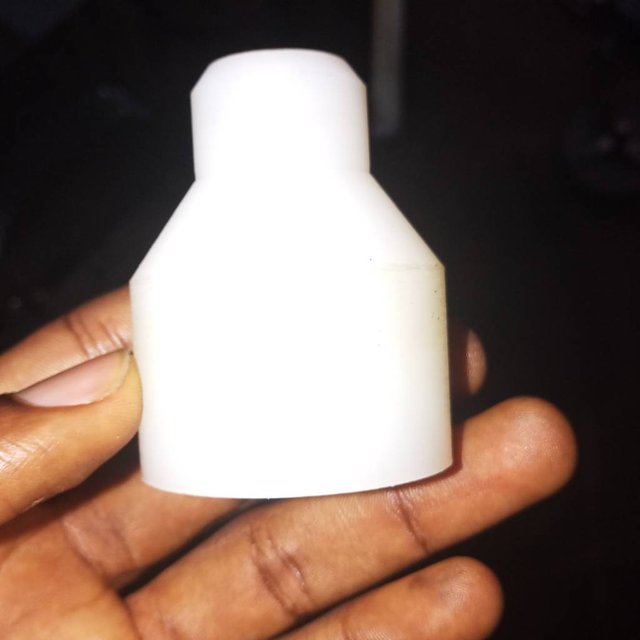
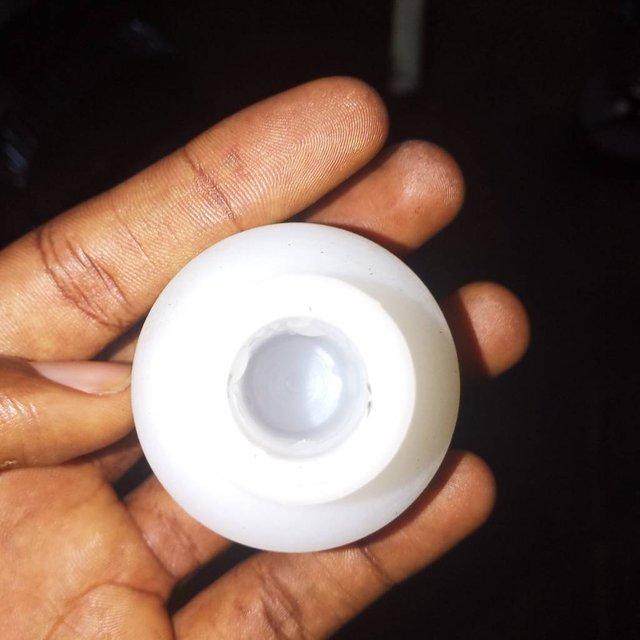
watch this video I made to see several operations being carried out

Conclusion
The reproduction of a machine part is not so easy as it involves precision and one being careful to prevent wastage of materials and also careful safety precautions were taken to achieve the reproduction of this machine part.
Some of it included coverall for the operator and safety goggle and boots to prevent the chips from flying into the eyes of the operator.
This machine part took about 6 hours to reproduce which is almost like half of the time I work in my workshop. I hope you enjoyed reading this?
If yes, feel free to talk in the comment box.

Reference
Knowledge is of course gotten from reading and listening and some of the books and sites I consulted were;
- lathe turning operation
- wiki turning
- machining handbook
- lathe operations; chamfering
- step turning on lathe
- high speed drilling
- Machine Tools - Dr. R. Kesavan
All images and videos were taken and made by me and are products of the Infinix zero 5 camera.
I have Always wondered how this companies ensure that the drinks they produce remain uncontaminated by the rust of metals but thanks to you @adetola now i know they use Polytetrafluoroethylene
Fantastic post with original images & videos: was worthwhile reading your post i learnt so much
Yeah PTFE does wonders in the drink production world.
Fantastic
Olamax Exchange is all about helping aspiring and existing steemians get to the top of their games with a number of groups on Whatsapp and Telegram. Below are the names of the groups and what they are all about:
IRISE (Whatsapp & Telegram): A community recommended for aspiring steemians. In this group, you can ask whatever question you may be having about steemit and get several answers almost immediately.
WHATSAPP: https://chat.whatsapp.com/80Q9T2gyD2PIzcoMLaAJe8
TELEGRAM: https://t.me/risenetwork
OLINKS (Whatsapp & Telegram): Here members can upload their articles links and get upvotes from other members and admins alike (50cents ‘calculated’ upvote from the admin during promos).
WHATSAPP: https://chat.whatsapp.com/Evnj1oqO4RfEduigZpxPNE
TELEGRAM: https://t.me/olinks
OLAMAX EXCHANGE (Whatsapp & Telegram): Here, members come to exchange their steemit earnings at current price. Transaction is swift and accounts are credited within 5 mins.
WHATSAPP: https://chat.whatsapp.com/BkYKNA3lZ7hLdJl0FtaFKy
TELEGRAM: https://t.me/Olamaxexchanger
E-mail which is [email protected]
WhatsApp number +2348156165413
Telegram: Olamax Exchange
Interesting and creative as usual. Just seeing this.....kudos
Thanks for visiting sir.. You are always welcomed here anytime.
Nicely written man
You almost a pro in manufacturing technology.... It's what would like to further on
Its a great if you love manufacturing... The society would love you helping out with machine parts.
It's cool but I am lazy person
CNC.... If you know
I can use manual but CNC has spoil me
So much to learn for just a day in your workshop, lol.
Haha.. Yeah, you don't stop learning in engineering.
Yeah, we learn everyday. Steem on sir!
As someone who either grows bugs and writes code, seeing the fabrication of real, tangible artifacts is like magic. Keep writing!
Haha... It isn't magic just unlike coding. I honestly believe that is magic.
Thanks for reading.
Then we should let our powers combine and do some CNC work and mystify everyone!
Hmm, nice. Would be cool to know how to do all these. I wouldn't have to look for a machinist whenever I have something I'd like to create.
There is always the option of a 3D printer, but the cheaper ones have limitations. Nice piece, enjoyed reading.
I don't think 3D printing will be an option against machining, not yet but it could if the materials used in printing are as strong as the materials we are machining.
But its a great angle to look from as an engineer, someday someone just might work on that.
Hmm, alright.
That is cool that you have a hands-on job like that, I enjoyed seeing the part come to life starting from that rough sketch.
This post was shared in the Curation Collective Discord community for curators, and upvoted and resteemed by the @c-squared community account after manual review.
Thank you.
Machining remains a saving grace to parts fabrication, esp ones that casting wouldn't be the best option for. I appreciate your effort to take us through step by step fabrication of this part of an important machine.....
I hope you get the deserve credit.
Yes.. Machining saves us so much stress than we can think of. imagine, having to prepare a cast just for this machine part what of the next and another. Its a life saver. Thanks for reading
wow this is nice oo
Thanks @olamax
The Art of creation indeed. Kudos man!
Thanks for being here.
You are welcome