Protecting Pumps, Valves, and Metal Surfaces in Fluid Delivery Systems
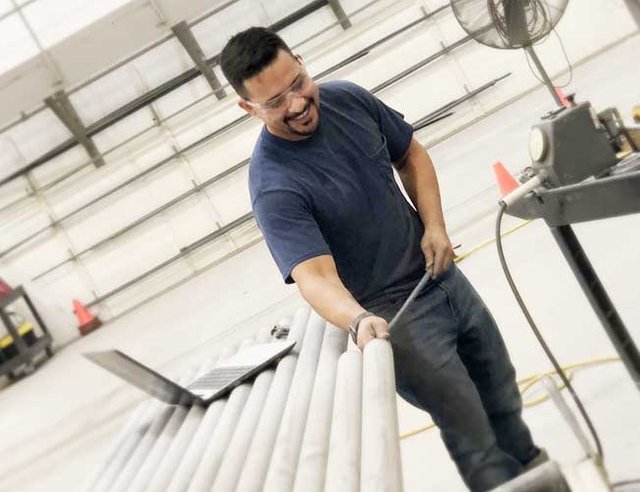
Industries that rely on fluid movement—whether it’s oil and gas, chemical processing, or water treatment—depend on durable, corrosion-resistant metal components. Pumps, valves, pipes, and tanks are vital infrastructure elements that transport industrial fluids under varying conditions. However, the exposure of these components to corrosive chemicals, extreme temperatures, and mechanical wear makes them vulnerable to degradation over time. To maintain efficiency and longevity, metal part manufacturers utilize advanced surface finishing techniques to protect these critical components from corrosion and wear.
The Impact of Corrosion on Industrial Equipment
Metal components in fluid delivery systems are constantly exposed to a range of corrosive elements, from acidic chemicals in processing plants to moisture in water treatment facilities. Corrosion weakens metal, leading to leaks, structural failure, and costly equipment downtime. For industries such as oil and gas, even minor corrosion can compromise the safety and efficiency of pipelines, pumps, and storage tanks. In chemical processing plants, the presence of aggressive solvents and acidic compounds accelerates metal deterioration, making protective coatings essential.
Industries that heavily rely on pumps, valves, and pipes include:
Oil and Gas: Pipelines, storage tanks, and drilling equipment need protection from corrosive hydrocarbons and extreme temperatures.
Chemical Processing: Harsh chemicals can erode unprotected metal surfaces, leading to leaks and contamination.
Water Treatment: Continuous exposure to moisture and chemicals makes corrosion-resistant coatings a necessity.
Food and Beverage Processing: Equipment used to transport liquids must meet strict safety standards while resisting corrosion.
Metal Surface Finishing Techniques for Corrosion Protection
To combat the effects of corrosion and mechanical wear, industrial metal parts undergo specialized surface finishing treatments. One widely used method is electroless nickel plating, a process that provides uniform, corrosion-resistant coatings without the need for electrical current. Electroless nickel coatings enhance the durability of pumps, valves, and other fluid-handling equipment by forming a protective barrier against corrosive substances.
Other popular metal coating processes include:
1. Thermal Spray Coatings – This technique involves applying a metal or ceramic coating onto surfaces using high-velocity spraying methods. It provides excellent wear resistance and corrosion protection, making it a top choice for pumps and valves exposed to aggressive fluids.
2. Powder Coating – A dry finishing process that applies a durable, protective layer over metal surfaces. Powder coatings offer resistance to chemicals, moisture, and mechanical wear while being environmentally friendly due to their low emissions.
For companies in need of metal coating for pumps in TX, selecting the right industrial coating service is critical to ensuring long-lasting equipment performance.
Wear-Resistant Coatings for Shafts, Gears, and Mechanical Components
Beyond corrosion resistance, metal components in industrial equipment must withstand continuous friction and mechanical stress. Wear-resistant steel coatings in TX provide enhanced durability for high-friction components such as shafts, gears, and bearings. These coatings reduce the impact of metal-to-metal contact, extending the life of moving parts and reducing maintenance costs.
Industrial sectors that benefit from wear-resistant coatings include:
Manufacturing and Heavy Equipment: Machinery components need protection against wear caused by repetitive motion and pressure.
Aerospace and Automotive: Engine components, turbines, and transmission parts require coatings that minimize friction and heat buildup.
Mining and Material Handling: Equipment subjected to heavy loads and abrasive materials benefits from specialized wear-resistant steel coatings.
Choosing the Right Coating Solution
Selecting an effective steel coating service in TX involves assessing the specific operating conditions of the equipment. Factors such as fluid type, temperature, and pressure play a role in determining the best protective coating. Many industrial coating services in Texas provide tailored solutions to safeguard metal parts from corrosion, mechanical wear, and environmental exposure.
The Long-Term Benefits of Protective Coatings
Applying the right protective coatings to industrial metal surfaces offers several key benefits:
Extended Equipment Lifespan: Coatings prevent premature degradation, reducing the need for frequent replacements.
Reduced Maintenance Costs: Protecting metal surfaces minimizes the risk of equipment failure, lowering overall maintenance expenses.
Environmental Responsibility: Choosing coatings with low environmental impact contributes to sustainable industrial practices.
Incorporating advanced protective coatings into your equipment maintenance strategy ensures that pumps, valves, and other metal components remain in peak condition for years to come. By investing in high-quality protective coatings, companies can optimize performance, reduce downtime, and enhance operational efficiency. The right metal coating not only extends the lifespan of industrial parts but also provides a cost-effective solution for maintaining equipment in harsh operating environments.