Automatic guided vehicles
The industry is constantly looking for new solutions in order to speed up and make the most of its production processes. AGVs are Automatic Guided Vehicles (AGVs) or, in other words, vehicles that run without a driver. One of the most innovative and important lines of business in ASTI is its AGV system, which has an extensive range depending on the guidance system, the loads to be transported and its management system.
Automatic guidance vehicles or AGVs are, in short, vehicles that do not need a driver to carry out the activity for which they were designed, the transport of punctual goods in industries.
To comply with their main characteristic of navigating or circulating as an autonomous vehicle without the need for human intervention as a pilot, these vehicles have different guidance systems and a complex system of control and management, which can differentiate two large groups: those whose management and control system does not communicate with the environment in which they move, that is, they are autonomous and the system only manages the fleet of vehicles making them work automatically and without interacting with the environment; or complex AGV systems, in which fluid communications with the environment are habitual and fundamental, since through these communications the orders of the vehicles and the movements to be carried out at all times are managed, communicating with the plant maintenance systems, automatic doors, automatic warehouses, as well as the company's management software, whether it be an ERP, an S, or an ERP.

Taking advantage of synergies
ASTI AGV systems can be incorporated in any company and adapted to any type of task and environment, retaining the option of being able to be used manually. Its use provides not only a reduction in costs and an increase in process efficiency, but also improvements in safety and quality. If one tries to make a comparison between humans and automatic guidance vehicles, one could say that there are different races or types of vehicles by two main points. Its physiognomy, i.e. the mechanics used to transport goods or the human body and its intelligence or management and control system, would be the invisible part of the system and would be in charge of articulating the vehicle, sending the nerve impulses, in this case digitised, necessary for the vehicle to raise its hands, advance 4 metres, reduce speed, stop, etc. ASTI has a wide range of automatic guidance vehicles, depending on the guidance system, the loads to be transported, the management system and the AGV implementation products, which contribute to the improvement of a base AGV. The company always seeks to offer the best solution for its customers, so that, whenever possible, they start from a conventional vehicle, manufactured in series by large companies engaged in the manufacture of industrial vehicles for the transport of goods, which meet the highest standards of quality, to which they provide a particular feature that their brothers do not enjoy: to be able to operate autonomously, without driver to guide him.
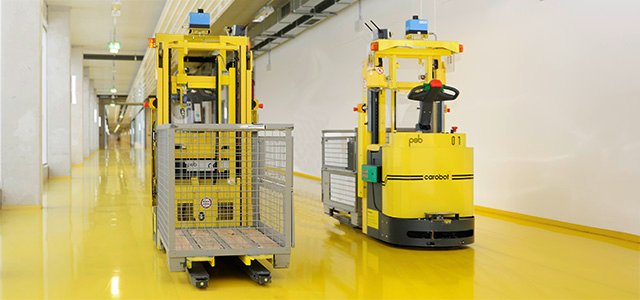
Standard mechanics has a series of advantages over custom mechanics, such as mass production, high quality standards, economy of scale of mass production, cost reduction, robust vehicles designed and manufactured to work in manual, fast spare parts service and maintenance, lower electricity consumption and greater stability.

Automate transport
The development of automation and robotics is enabling small and medium sized companies to incorporate AGV automatic vehicle guidance systems into their production processes.
Companies are demanding to handle the necessary materials faster, more precisely and more accurately. Knowledge of the production process and control of its expenditure are essential if you want to maintain a position in the market. There is a growing tendency to focus all energies on creating and expanding business, without forgetting that the production process itself must provide high quality, at a low cost.
On many occasions, being first is better than being bigger. Many products have very short life cycles and leave no room for mistakes. Everything has to go fast, and at a lower cost. This requires maintaining complete control with constant access to information from the production system and processing and managing this information to get the most out of the company's resources.
One of the problems to solve is the movement of goods within the production process, it is essential to have to move from one side to other raw materials and semi-finished products.
If the movement of these goods is observed, many of them follow common routes, and personnel are needed to move them from one place to another. These personnel perform repetitive and monotonous tasks, are demotivated by lack of objectives at work, have no goals to achieve, often have excessive confidence in the vehicles they drive, and an error in these processes generates economic losses, and in some cases, personal misfortunes. In the same way that we tend to automate complex processes, we can consider transport automations.
Until recently, the development of robotics could not cover the need to automate these tasks, with the latest advances in this field, ASTI can address this problem with guarantees of success, in addition, automate transport tasks using autonomous vehicles, is more flexible than traditional transport systems, such as belts, chains and other fixed installation devices, and above all, allowing this way have a machine that in manual mode behaves like a conventional machine, and in automatic mode is able to perform transport tasks without the need for a driver.
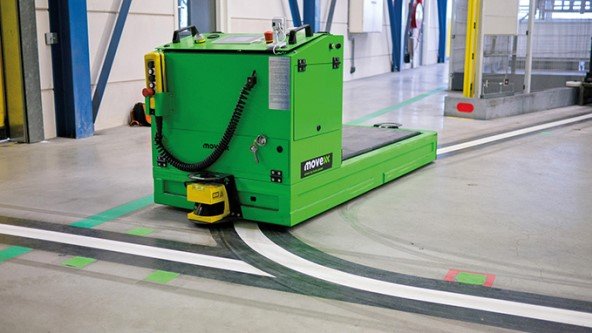
An automation of this type only forces to work in a more disciplined way, but the amount of information and reaction capacity that it creates, more than compensates the 'effort' of 'disciplining' the production. Not only are improvements obtained in transport; some of the advantages obtained from this type of installations can be enumerated:
Increase speed and productivity in the handling and handling of materials.
Increased safety for personnel working in the plant; this system makes it possible to define what additional levels of safety are required.
Considerable savings in the cost of damages caused to the transported goods.
Savings in the maintenance of the vehicles, since the programmed driving is the optimal one in every moment.
Energy savings in the plant, since thermal leaks are considerably reduced.
To evaluate economically and objectively all the mentioned points is difficult, they depend very much on the company and on the proposed solution.

Steemit is expanding to other blog ecosystems, will soon be official with Smart Media Tokens and is already possible for WordPress thanks to the steempress plugin, a revolutionary initiative. If you wish to support the project I invite you to vote for @steempress as a witness by clicking here
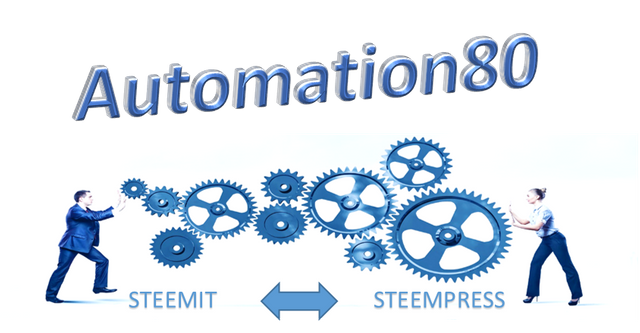
Posted from my blog with SteemPress : https://automation80.000webhostapp.com/2018/10/automatic-guided-vehicles
I upvoted your post.
Cheers to you.
@Pinoy
Posted using https://Steeming.com condenser site.