A Journey through Stainless Steel
Stainless Steel (SS)
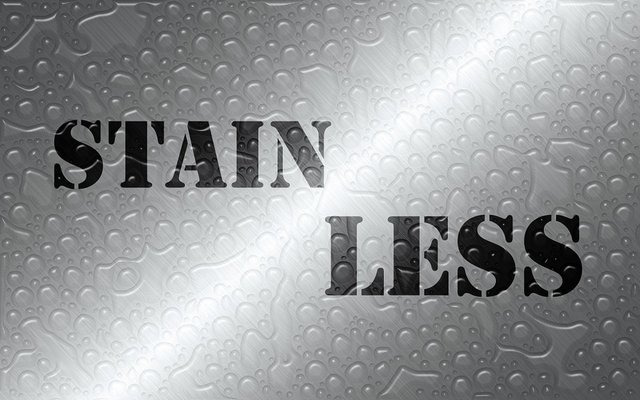
Stainless Steel
Oblivious to our sight or touch, we use or come into contact with a certain steel product daily. Be it in the kitchen, while driving or even while holding our phone, we unconsciously encounter steel. This post is to elaborate on the most used and versatile type of metal out in the everyday world, Stainless Steel.
Everyone knows that Stainless Steel is a metal that does not corrode at all or to a certain degree, dependent upon the degree of treatment it is been given. However, this isn’t going to be that type of post. I am going to be taking you on a journey into the different branches of Stainless Steel and then diving into the microscopic world of each of these for us to understand how it is able to be unaffected by corrosion over long periods of time.
Stainless Steel is a common name originally used in industry but then also used domestically to describe a metal that meets the following chemical constitutional requirements:
11% or more Chromium, a small (close to minute) amount of Nickel as well as more than 50% Iron, and the remainder a combination of other types of metals and elements, such as carbon.
Chromium between a range of 11% to 27% is often used in a steels composition to facilitate corrosion resistance. Chromium and chromium alloys allow passivation (a process to prevent corrosion, which will be explained later) to occur and has certain environmental resistances, thus explaining why it needs to make up such a large portion of Stainless Steels total chemical makeup. Iron, that is consisted in its makeup, is used to provide the properties that are associated with steel such as metallic properties, its shine, magnetic properties and so on. As a mathematical description:
Iron+Chromium+Nickel+Other Elements=Stainless Steel
Stainless Steel can be branched into many different forms, namely
Austenitic SS
This is a branch of stainless steel that contains roughly 16-26 % chromium and around 6-23 % nickel and is described to have a face centered cube structure, commonly abbreviated in the engineering world as FCC. This branch of steel is considered an extremely special type of stainless steel simply because it is non-magnetic. It also displays strong qualities such as being extremely tough and very ductile. Austenitic Stainless Steel is referred to as a Type 304 which is a AISI type. AISI (American Iron and Steel Institute) features all information regarding all types of steel. To help with the identification of steel, certain naming methods were introduced, thus one of the products of this system is referring to Austenitic Steel as Type 304. The table at the end of the descriptions of these branches can be viewed for a more detailed breakdown in information. Type 304 is the most widely used branch of steel worldwide due to its cost factor as well as workmanship. Type 304L, which is a more advanced and furthered treated version of Type 304, is preferred for environments were corrosion is a problem, thus Type 304L has a high resistance to corrosive environments. Applications of Austenitic steel include uses in domestic homes such as wash basins, and sinks and even certain kitchen equipment such as food processors.
Ferritic SS
This steel grade is referred to as Type 430, according to the AISI. The general composition of this branch of stainless steel is around 12-25 % Chromium in its total chemical composition, and is considered the simplest form of SS as its chemical configuration is not as complicated as the other branches. Due to this reason, Ferritic SS are not suited for harsh corrosive environments and are only used for moderate corrosive resistance. This type of SS is again used for domestic uses but this is commonly found inside clothing and dish washing machines.
Martensitic SS
Containing a chemical composition of approximately 6-18 % Chromium and around 2 % Nickel, Martensitic SS is referred to as Type 410. It is a strong and hard branch of Stainless Steel that is also magnetic in nature. This branch is used for milder corrosive environments than compared to the previous 2 as applications are for combat based, such as blades and knife as well as industrial for products such as bearings that are corrosion resistance.
Duplex SS
This branch of Stainless Steel has “duplex” in its name because in its microstructure, it has 2 phases that consist of grains of Ferritic and Austenitic Stainless Steel that are almost equal in its chemical composition, that is, 50 % Ferritic SS and 50 % Austenitic SS. As a result, it contains properties of both branches of Stainless Steel.
Precipitation Hardening SS
Commonly called Type 17-4, Precipitation Hardening Stainless Steel has a higher level of strength of any other branch and has a higher corrosive resistance when compared to that of Martensitic Stainless Steel. The applications of this form of steel is used for a higher level of specialized uses such as defense mechanisms in war as well as in aeronautical engineering as for aircraft production.
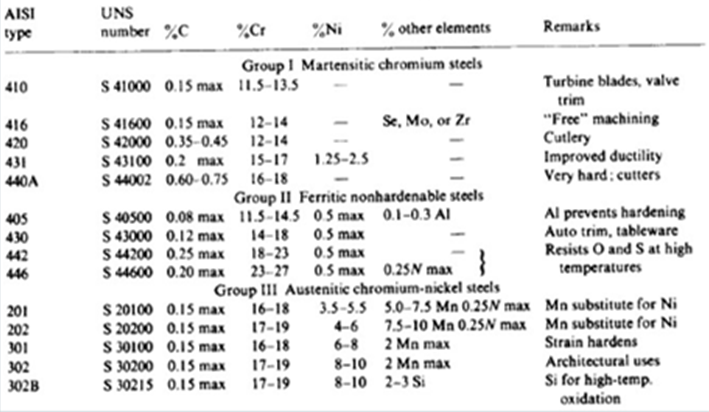
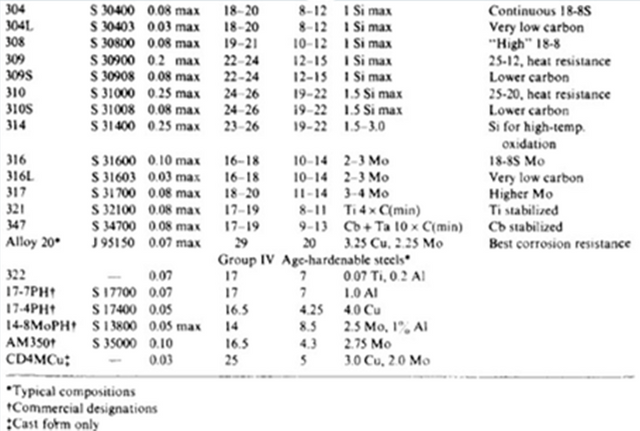
AISI Table
Stainless Steel Corrosion
Stainless Steel does not rust or corrode as easily as ordinary steel due to its protect resistance layers as well as its chemical composition. There are certain types of corrosions that do affect Stainless Steel and they are grouped into 2 lots:
- Wet and Dry Corrosion
- Room and High Temperature Corrosion
We will be discussing the effects of Wet Corrosion, which is the most common occurring corrosion among Stainless Steel. It is categorized into:
Uniform Corrosion
Also referred to as General Corrosion, this type of corrosions occurs on the surface of a metal and then proceeds uniformly throughout the metal. An example would be Atmospheric Corrosion. This form of corrosions ensures maximum metal loss and greatly exceeds metal loss of any other type of corrosion. It is not dangerous to the human body and can have its rate of metal consumption measured in a laboratory. It should be noted however, that this form of corrosion can only occur when there is an overall breakdown of a passive film that is found upon a steel surface for corrosion resistance.
Galvanic Corrosion
This form of corrosion occurs when 2 unlike or dissimilar metals are electrically contacted with one and other and are also immersed in an electrolyte. When this process occurs, a galvanic couple will form, thus one of the two metals will become an anode while the becomes a cathode. The metal that becomes an anode will now corrode away faster than it would have had it being alone, while the opposite will occur for the cathode. This corrosion is a sort of “sacrificial” corrosion as one must be depleted to preserve the other.
For Galvanic Corrosion to be initiated, the following requirements need to be satisfied:
- 2 dissimilar metals must be used
- There must be metal to metal contact
- Metals must be partially submerged in the electrolyte (elctrical conductive solution)
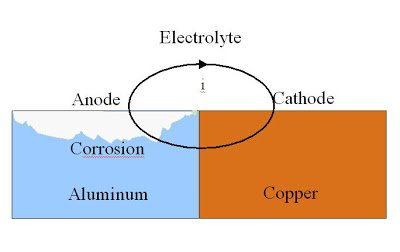
Galvanic Corrosion
If any of these conditions are not met, Galvanic Corrosion will not be carried out.
Pitting Corrosion
Localized corrosion on a metals surface that produces small holes in the metal in a specific area only, is referred to as Pitting Corrosion. This corrosion, just as uniform corrosion, occurs when the environment uses its corrosive nature to penetrate the passive film but the only difference is that this form of corrosion only affects a few areas of the surface rather than the entire area. Halogens often will penetrate the passive films of the stainless steel.
Intergranular Corrosion
Formation of chromium carbides at extremely high temperatures (450-860 °C) will lead to Intergranular Corrosion. By carbides forming in the grain boundary, the overall chromium content decreases and this will lead to a lower corrosive resistance around the grains and thus the steel. This form of corrosion is mainly found in Austenitic Stainless Steel.
Erosion Corrosion
Erosion Corrosion forms as a product of a mixture of fluids travelling at high velocities and a naturally aggressive chemical environment. Fluid flow may carry away any corrosion protective films that may have being intended to protect to the surface of the steel or material and thus making that area susceptible to Erosion Corrosion.
Chemical Corrosion Resistance
Chromium:
- Chromium forms an essential part of the passive film found upon a metals surface.
- The relationship between chromium content and corrosive resistance is directly proportional, meaning, the higher the amount of chromium in the metals chemical makeup, the higher the level of corrosive resistance.
- For a level of high corrosion resistance, that is, a strong passive film, a chemical composition containing 25-30 % Chromium is efficent.
Nickel:
- Nickel is often related to stress corrosion cracking.
- When Nickel is increased to above 10 % of a materials chemical composition, its stress corrosion cracking resistance increases.
Manganese:
Although the effects of manganese is not well recorded, we do know that when it chemically combines with sulphur, it forms sulphides. Sulphides, however, are known to have a substantial increased effect on corrosion resistance.
- with the introduction of molybdenum to the chromium-iron-nickel mixture will create a higher added level of resistance to pitting corrosion.
- Increases a materials resistance to crevice corrosion
Since corrosion can not be fully stopped, there are methods to prevent it from occuring at all. The following methods, with decriptions, are below:
Passivation:
An extremly thin layer (with a thickness of microns) consisting of Chromium oxide is formed on the surface of a metal and thus encloses the metal from the environment, isolating it from corrosive attributes. The thin layer of film placed upon the metals surface is referred to as a Passive Film.Polarization:
The chemical potential driving force in a reaction is removed. When this is done, the thermodynamical force that drives ions into a solution is reduced and this is referred to as polarization. For example, if there are not enough ions available for a recation at a cathode, the corrosion potential at the cathode will decrease, therefore, corrosion may not take place or may take place to a small degree.Sacrifical Layer:
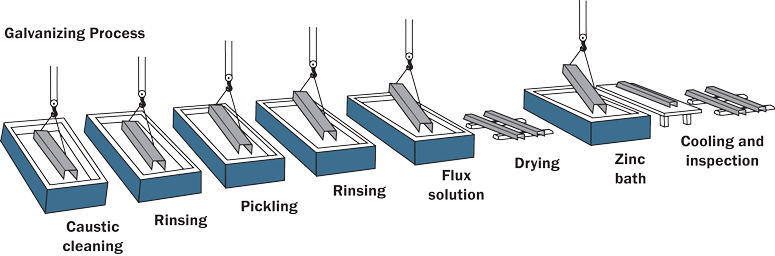
The Galvanizing Process
This method is often referred to as Galvanization of Steel. A sheet of metal is dipped into molten zinc and removed. When removed, it has a thin layer of zinc all around the metals surface. Zinc will now become the anode and any exposed steel that was somehow not coated by the zinc becomes the cathode. Because such a large anode will need to be served by such a small cathode in comparison, the produced corrosion rate will be extremely slow.
Images are linked to their sources in their description
The End
References:
[1]https://en.wikipedia.org/wiki/Stainless_steel
[2]https://www.bssa.org.uk/faq.php?id=10
[3]https://www.bssa.org.uk/faq.php?id=9
[4]sassda.co.za/stainless-steel-and-corrosion/
[5]https://www.pennstainless.com/general-product-information/corrosion-prevention/
[6]sassda.co.za/stainless-steel-and-corrosion/
Being A SteemStem Member